
Table of Contents
Critically examining the designs and details of available products/techniques and discussing future developments.
14 August 2018
1. Introduction
Printed circuit boards (PCBs) are becoming an ever more important part of today’s technology, creating more efficient devices and allowing them to be smaller and more compact than ever. Currently, the most common method of construction is using sheets of copper that have been etched to replicate a circuit design and then laminated onto a non-conductive material. This review will explore and analyse the advanced techniques that help detect and prevent and minimise electromagnetic interference (EMI) that are found in PCBs. EMI is the most detrimental aspect to a PCBs reliability and efficiency. The techniques used include: the prevention of EMIs through design, EMI Shielding and finally the production of simulation software. By exploring the effectiveness and practicality of said technologies, we will be able to view how EMIs can be reduced and controlled to create more reliable PCBs in the future.
2. Astute PCB design
The first measure taken to reduce, and control EMI is through the physical design of the PCB and the position and or methods used to connect said PCB to enclosures (Compute cases, Vehicle shells, etc), PCB chassis and or cables. The chassis, enclosures and cables unfortunately share the same properties as antennas, resulting in an increase of EMI with in the PCB circuitry. Because of this, the need for smart PCB design is essential.
The chassis and or enclosure that surrounds and connects a PCB to the device, is often used as a ground location for the PCB; It is generally connected only to the ground layer of a PCB using 4 screw locations [1] . When the PCB is attached to the chassis electrically the EMI measured was significantly increased compared to when it was electrically separated. This is because the chassis increases the area in which interference can be absorbed. To reduce the antenna like effects of the chassis, it is preferable to reduce the current that flows through the connection from the PCB to the chassis and or ground [1]. One way to achieve this, is to attach bypass capacitors close to the connection point [1].
As PCB designs and requirements get more complicated and dense with components, it will be important in the future to optimise the layout and position of components and connections in a PCB. While this testing shows promise for simple manipulation of ground connections, more complex components such as tracers and vias need to be evaluated as they are the most common component of a PCB and therefore, will have a larger impact on EMI.
3. EMI Conformal Shielding
2.1 Solid Metallic shell
Fully encasing a PCB in a metal shell is a common and simple way of protecting the circuit from external EMI, however this can result in noise resonating within the shell due to the internal components and signals [2]. To prevent this resonance, special shells that possess side wall openings are being implemented. Because resonant frequencies are determined by the dimensions of the shell, opening the side walls would result in a shift in resonant frequency [2]. It will also allow any resonant signals to escape so that they do not continue to reflect inside the shell.
The shell tested with the addition of side-wall openings resulted in a dramatic improvement. EMI was reduced by 7dB, depicting a significant contribution to EMI is the internal resonance of the shell/circuit [2]. Furthermore, if the shell is formed from iron, and steel shields are directly applied to the CPU, interference can be reduced even more [3].
Metal shielding is one of the easiest and simplest techniques to block incoming interference and can be utilised on almost every PCB application. However, with increased weight, bulk, expense and quantity of the materials used in production it is a somewhat unappealing technique.
An upcoming substitute to the traditional metal lid, is thin metal layers that conform directly to the module and or PCBs surface. There are multiple methods used to deposit the layers onto the PCB including electroless plating and sputtering. These techniques offer similar EMI shielding effectiveness as metal lids but offer a reduced overall foot print and usage of material.
2.2 Electroless plating
Electroless plating is a consistent, and cheap technique that proves to be one of the most commonly used approach to encase an object in a thin layer of metal [4]. Electroless plating using copper and nickel is a new technique being utilised to create efficient EMI shields [4]. The metals used in this plating procedure must have high electrical conductivity properties as this aids in both reflection loss and absorption loss [4]. Copper has exceptional performance in these fields as well as a low price. Nickel provides a cheap solution to prevent an oxidation layer from forming on the copper layer, while also enhancing the EMI alleviation properties of the shield [4].
To optimise the adhesion of the copper and nickel materials, it is important to perform a ‘swelling’ step for 15 minutes [4] creating a rough plating surface. Etching for 5 minutes can improve on this [4]. Extending these periods will result in a surface that is too rough, resulting in crack initiation and stress concentration, decreasing adhesion [4]. An increase in the thickness of the copper layer results in a proportional shielding increase. However, increasing the nickel layer thickness does not improve performance [4].
Using electroless plating will prove to be a simple and efficient way to create conformal shielding, however, if the surface being plated is not perfectly flat the process will not work efficiently. Because of this another layer would still need to be created around a PCB before electroless plating can be implemented.
2.3 Metallic spray/ Sputtering
To remove the need for an extra flat layer encasing the PCB, a technique has been developed, allowing a shielding material to be directly sprayed onto the PCB. A metallic based ink is used as it is highly electrically conductive, which is essential to successful EMI shielding [5]. This ink is thin enough to be easily sprayed onto epoxy moulded surfaces, in turn creating an invariably thin layer on the device [5]. Nozzle-less, ultrasonic spray gun technology is implemented to allow a reduction in waste material and increase the consistency in material dispersion [5]. In turn allowing optimal and repeatable shielding.
The ink used in this technology is inorganic, resulting in an increase in conductivity, that can be comparable to copper. It also implemented additives that were impermeable to magnetic energy, increasing the EMI reduction performance [5]. Far field measurements (used to measure EMI) depicted that the ink performed eighty percent better than classical organic-based conductive inks [5]. The measurements were taken at similar ink thicknesses (3-5 micro-meters) resulting in better PCB component and etching visibility, layer uniformity and reduction in ink usage. This technique of spraying allowed superb coverage over the device, including the corners and edges of the PCB. The top to sidewall thickness ratio of 1:0.5 was achieved using a pitch-to-height ratio of 1:1 [5]. This is vital for efficient EMI reduction as any gap found in the shielding can allow interference through.
This shield spraying technology allows for the smallest footprint and or package as no extra shell must be created around the PCB, resulting in a reduced physical footprint of the device itself.
4. EMI Simulation
When a PCB is being developed, EMI is unable to be predicted/ measured. Therefore, only when the PCB was printed, electromagnetic interference of the PCB was able to be measured. If the EMI was too high or not within regulation, the PCB would have to be re-designed costing more money and time. EMI simulation technology has been created to avoid this waste in resources and make PCB production much more efficient and predictable.
To make the simulation process easier and more accurate, only components that have a large current and voltage are included in the simulation [6]. The currents from the selected components are calculated with a circuit simulation programme, a three dimension model of currents is then created [6]. From here they calculate the radiated far field (RFF). The simulation results are then compared to a real world test that takes place in an EMC chamber, a non-reflecting chamber that allows accurate measurements of EMIs.
There were several tests undertaken: trivial circuits, more complicated PCBs and a test board with varying trace designs used. The largest under-prediction was 5dB, while the largest over-prediction was 10dB [6]. However, majority of these errors were due to imperfections with the testing equipment.
As computers become more powerful, EMI simulations will become more precise as a result. In turn, the necessity for said software will grow and become more useful than ever. Because EMI simulation can reduce waste in resources due to less time and money spent in the design phase, and with no real downside, EMI simulation will prove to be a key aspect to PCB design in present and future technologies.
5. Conclusion
Electromagnetic interference in printed circuit boards can be reduced and controlled using an array of different techniques and technologies. The initial step includes smart PCB design, reducing current flow from PCB to chassis connections. Residual EMI can be removed and filtered using an array of shielding technology, the easiest technique is a hard metallic shell that uses plenty of expensive, bulky material. Reducing bulk can be achieved by implementing electroless plating on a more slim fitting shell. While the most cost efficient and compact technique is to spray non-organic, metallic ink directly onto the surface of the PCB. After all these techniques have been implemented physically or in design we can produce a simulation to further reap the rewards of our EMI prevention techniques. The need for these technologies is becoming ever more prevalent as the speed of operation of printed circuit boards increases. Because of this increase, higher component densities occur and in turn an increase of EMI in said PCBs.
References:
[1] H. Funato and T. Suga, “A Study on Correlation Between the PCB Layout and EMI from Chassis,” in 2007 IEEE International Symposium on Electromagnetic Compatibility, 2007, pp. 1–5.
[2] M. Liao, A. Lin, and C. Huang, “A new resonance-eliminating EMI conformal shielding with side-wall openings,” in 2017 12th International Microsystems, Packaging, Assembly and Circuits Technology Conference (IMPACT), 2017, pp. 118–121.
[3] T. Tang and C. C. Ho, “EMI suppression for high-speed PCB,” in 2009 International Waveform Diversity and Design Conference, 2009, pp. 168–172.
[4] F. Jiang, M. Li, and L. Gao, “Research on conformal EMI shielding Cu/Ni layers on package,” in 2014 15th International Conference on Electronic Packaging Technology, 2014, pp. 227–230.
[5] X. Cao, A. Sun, D. Maslyk, J. Gao, Q. Zhuo, and J. Choi, “Effective EMI shielding for semiconductor packages through novel conformal coating,” in 2018 China Semiconductor Technology International Conference (CSTIC), 2018, pp. 1–5.
[6] H. Heeb, A. Ruehli, J. Janak, and S. Daijavad, “Simulating electromagnetic radiation of printed circuit boards,” in 1990 IEEE International Conference on Computer-Aided Design. Digest of Technical Papers, 1990, pp. 392–395.
What Students Are Saying About Us
.......... Customer ID: 12*** | Rating: ⭐⭐⭐⭐⭐"Honestly, I was afraid to send my paper to you, but you proved you are a trustworthy service. My essay was done in less than a day, and I received a brilliant piece. I didn’t even believe it was my essay at first 🙂 Great job, thank you!"
.......... Customer ID: 11***| Rating: ⭐⭐⭐⭐⭐
"This company is the best there is. They saved me so many times, I cannot even keep count. Now I recommend it to all my friends, and none of them have complained about it. The writers here are excellent."
“Order a custom Paper on Similar Assignment at essayfount.com! No Plagiarism! Enjoy 20% Discount!”
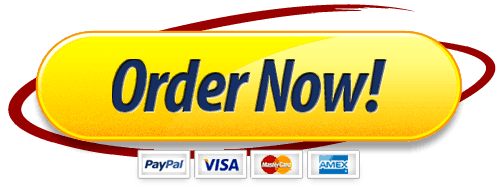