
Description
The assignment describes in detail the measures of Quality of Fit (GOF) in AMOS analysis Explore the literature and / or Google to describe factors like Chi-Square, CFI, GFI, NFI, RMSEA, and others. To write in simple and clear language, and provide references between (2016-2020) The curriculum talks about quantitative analysis, and I attached an article that he provided as an example on page 1131 of the subject teacher and he would like to understand what it is, but we write from other sources
Critical linkages among TQMfactors and business resultsIsmail SilaDepartment of Finance and Management Science, College of Commerce,University of Saskatchewan, Saskatoon, Saskatchewan, Canada, andMaling EbrahimpourGabelli School of Business, Roger Williams University, Bristol,Rhode Island, USAAbstractPurpose – To empirically investigate the relationships among critical TQM factors and businessresults.Design/methodology/approach – Twenty-three hypotheses regarding the relationships amongTQM factors and business results have been developed through literature review and tested usingstructural equation modeling (SEM). The study utilized survey data obtained from US manufacturingcompanies.Findings – Provides information about the results of each hypothesis, their implications, and howthese findings compare to previous studies. Pays special attention to the relationships between TQMfactors and business results and discusses findings in this area by offering insights from 22 previousstudies that analyzed TQM-performance relationships.Research limitations/implications – Researchers could use the results of this study to explorevarious related hypotheses in more detail and improve the accuracy of future empirical qualitymanagement studies. The study makes specific recommendations for such future studies. There werealso some research limitations. For instance, the data were obtained through mail survey and relied onthe perceptions of the respondents.Practical implications – The results of this study can be used by managers to prioritize theimplementation of TQM practices. For instance, those practices that are found to have a positiveimpact on business results can be recommended to managers so that they can allocate resources toimprove these practices to get the best results.Originality/value – This study conducts a comprehensive review of the literature to develop factorsof critical TQM practices and business results, and unlike most previous studies, it uses multiple,distinct indicators for each factor to test an elaborate SEM model of the relationships among thesefactors.Keywords Total quality management, Manufacturing industries, United States of America,Linear structure equation modellingPaper type Research paperIntroductionThe critical factors of TQM can be described as best practices or ways in which “firmsand their employees undertake business activities in all key processes: leadership,planning, customers, suppliers, community relations, production and supply ofproducts and services, and the use of benchmarking …” (Australian ManufacturingCouncil, 1994, p. 1). The purpose of this study is to empirically investigate therelationships among these critical TQM factors and their impact on business results.The results of this study can be used by managers to prioritize the implementation ofThe Emerald Research Register for this journal is available at The current issue and full text archive of this journal is available atwww.emeraldinsight.com/researchregister www.emeraldinsight.com/0144-3577.htmCritical linkagesamong TQMfactors1123International Journal of Operations &Production ManagementVol. 25 No. 11, 2005pp. 1123-1155q Emerald Group Publishing Limited0144-3577DOI 10.1108/01443570510626925these practices. For instance, those practices that are found to have a positive impacton business results can be recommended to managers so that they can allocate theircompanies’ resources to improve these practices to get the best results. Researcherscould also use the results of this study to explore various related hypotheses in moredetail and improve the accuracy of future empirical quality management studies.The rest of this study is organized as follows: the next section provides an overviewof the previous studies conducted in this area followed by a discussion of the modelvariables and the hypotheses regarding the relationships among these variables. Thenthe methodology used, the statistical analyses conducted, and results are conveyed.Finally, the last section discusses results and conclusions, as well as the implications ofthe study for managers and researchers.Literature reviewThe previous survey-based TQM studies formed the basis for the current study. Table Iprovides a comparison of eight such previous studies.The first survey study that attempted to identify the critical factors of TQM thatmust exist in a business unit to achieve effective quality management is that by Saraphet al. (1989). This study used organizational and managerial aspects of the works of anumber of quality management practitioners such as Deming, Juran, and Crosby toorganize and synthesize the critical factors identified by them. Saraph et al. (1989) alsodeveloped measures of each critical factor and overall organizational qualitymanagement. A similar study was conducted by Anderson et al. (1994) who developedseven TQM factors to represent the “Deming management method”. The relationshipsbetween these factors were later empirically analyzed by Anderson et al. (1995).In addition to these studies, various other empirical studies attempted to develop anappropriate set of critical TQM factors representing an integrated approach to TQMimplementation. The objective of a study by Adam (1994) was to identify the qualityimprovement and productivity improvement techniques that have the greatest impacton performance quality and operational and financial performance. This study found astrong relationship between quality improvement approach and performance quality,as well as operating and financial performance. Adam’s (1994) study was furtherexpanded by Adam et al. (1997) to compare the relationship between TQM factors andproduct quality and financial performance across three regions, Asia/South Pacific,Europe, and North America. The study found that the nine TQM factors extractedacross three samples followed a similar pattern, where factors most important in oneregion were also the most important factors in other regions. However, all three regionswere different from each other in terms of the relationships between the TQM factorsand performance.Another cross-country study was conducted by Rao et al. (1997) in India, China andMexico, which found that the importance given to various TQM factors was consistentin the three countries. In addition, this study found that quality results, measured bylevels of scrap and rework, productivity, market share, and so on, were notsignificantly different in the three countries.Unlike Adam et al. (1997) and Rao et al. (1997), who investigated the TQM factors inmultiple countries, most of the other similar studies focused on only one country. Forinstance, Flynn et al. (1995) developed a set of TQM factors using the relevant literatureand tested relationships between these factors and performance measures using pathIJOPM25,111124Study TQM factors Source of TQM factors Performance measuresPrincipalanalysistechnique SampleSaraph et al.(1989)Role of divisional topmanagement and qualitypolicy, role of qualitydepartment, training,product/service design, supplierquality management, processmanagement/ operatingprocedures, quality data andreporting, employee relationsBased on philosophies andprescriptions of qualitypioneers such as Juran,Deming, and CrosbyNone Factor analysis 162 manufacturing and servicecompaniesAndersonet al. (1995)Visionary leadership, internaland external cooperation,learning, process management,continuous improvement,employee fulfillmentBased on teachings ofDemingCustomer satisfaction Path analysis 41 manufacturing companiesFlynn et al.(1995)Top management support,customer relationship, workattitudes, work forcemanagement, supplierrelationship, product designprocess, process flowmanagement, statisticalcontrol and feedbackBased on a review of theliteraturePerceived quality marketoutcomes, competitiveadvantage, percent passedinspection with no reworkPath analysis 42 manufacturing companiesAhire et al.(1996)Top management commitment,supplier quality management,supplier performance, customerfocus, SPC usage,benchmarking, internal qualityinformation usage, employeeinvolvement, employeetraining, design qualitymanagement, employeeempowermentBased on a review of theliteratureProduct quality Path analysis 371 manufacturing companies(only from the motor vehicleparts and accessories industry)(continued)Table I.A comparison of some ofthe previous empiricalTQM studiesCritical linkagesamong TQMfactors1125Study TQM factors Source of TQM factors Performance measuresPrincipalanalysistechnique SampleAdam et al.(1997)Employee involvement, seniorexecutive involvement,employee satisfaction,compensation, customers,design and conformance,knowledge, employee selectionand development, inventoryreductionMainly based on Benson et al.(1991) and the 1991 BaldrigeAwardPerformance quality, financialperformance, annual employeeturnover rateStepwiseregression977 manufacturing and servicecompaniesDow et al.(1999)Workforce commitment,shared vision, customer focus,use of teams, personneltraining, co-operative supplierrelations, use ofbenchmarking, use ofadvanced manufacturingsystems, use of just-in-timeprinciplesBased on the 1994 BaldrigeAward criteria, the DemingPrize criteria, the 1993European Quality Awardcriteria, the 1994 AustralianQuality Award criteria, andMade in Britain (1992)Product quality Path analysis 698 manufacturing companiesWilson andCollier (2000)Leadership, strategic planning,human resource developmentand management, informationand analysis, processmanagementBased on the 1995 BaldrigeAwardCustomer focus andsatisfaction, financial resultsPath analysis 160 manufacturing companies(only from the automotiveindustry)Kaynak(2003)Management leadership,training, employee relations,quality data and reporting,supplier quality management,product/service design,process managementBased on Saraph et al. (1989) Financial and marketperformance, qualityperformance, inventorymanagement performancePath analysis 214 manufacturing and servicecompaniesTable I.IJOPM25,111126analysis. Other similar studies have been conducted that explored such relationships(Anderson et al., 1995; Rungtusanatham et al., 1998), and they also mostly used a pathanalytic model. In addition, some studies such as those by Anderson et al. (1995) andRungtusanatham et al. (1998) focused only on one theory of quality management,namely the Deming management method.A review of the literature suggests that most of the TQM factors found in theempirical quality management literature are comprised of more than one indicator,which favor the use of a latent variable model. For instance, it is posited in the currentstudy that the information and analysis factor can be measured by five indicators:performance measurement and analysis, information management, benchmarking, useof information technology, and quality tools. Most of the researchers in this areaoperationalized such factors by grouping all the items related to them together.However, there are indeed sufficient differences among many of the indicators thatwarrant the use of a latent variable model. Two TQM related studies that did use alatent variable model include Forza and Filippini (1998) and Kanji and Wallace (2000).However, Forza and Filippini (1998) tested their model using a limited number of TQMfactors and only used conformance and customer satisfaction as the performancemeasures. The model was tested using 43 companies located in Italy. On the otherhand, Kanji and Wallace (2000) used the Kanji business excellence model as aframework to create latent factors and test their impact on “business excellence”. Themodel was tested using a sample of 61 European manufacturing and servicecompanies.The use of a latent variable model where the factor loading of each indicator on itscorresponding factor can be assessed allows researchers to evaluate the indicators’relative significance for the successful implementation of that particular factor. Someof the advantages of latent variable models over path analysis are the following: unlikepath analysis, latent variable models use latent constructs (factors), which could helpresearchers to more fully assess each construct and explain phenomena moreaccurately. Thus, multiple indicators per factor are used in latent variable modelanalysis versus one indicator per factor in path analysis. Secondly, in latent variablemodels, the estimation of both measurement error and prediction error (not possiblewith most other multivariate techniques) can eliminate bias during model testing. Onthe other hand, path analysis assumes that there is no measurement error in theindependent variables. However, most single variables have some degree ofmeasurement error, which could cause bias if they are not taken into considerationduring model testing. In addition, in path analysis, the dependent variables maycontain errors of measurement, but they are assumed to be present only in the residualterms of the model equations (Raykov and Marcoulides, 2000).The proposed structural equation modeling (SEM) model in this study is differentfrom most of the other models tested in this area not only because it is a latent variablemodel but also because it integrates the variables and relationships tested by previousstudies and derives from them. It is thus very comprehensive in terms of the number offactors and indicators used and hypotheses tested. Finally, unlike many previousstudies that mainly focused on one or two types of business results measures, thecurrent study used a composite of key business results that balances the requirementsof all stakeholders including customers, employees, stockholders, and suppliers andpartners (NIST, 2002).Critical linkagesamong TQMfactors1127Model variables and hypothesesAn extensive review and classification of the relevant empirical literature revealedthat, in a broad sense, the following seven TQM factors were the most often extractedfactors: leadership, strategic planning, customer focus, information and analysis,human resource management, process management, and supplier management. Thesefactors are listed in Table II with their associated indicators. Using the practice ofHandfield et al. (1998), several indicators used in the Malcolm Baldrige NationalQuality Award (MBNQA) that are not generally emphasized in the literature have alsobeen included to measure some of the factors (NIST, 2002).Business results is the eighth factor (F8) used in this study and represents theperformance measure in the latent variable model. Table II also lists the four indicatorsmeasuring this factor and the items used to operationalize each of the indicators.SEM requires that the proposed relationships among variables in a model besupported by the relevant literature. Extensive conceptual, anectodal, and empiricalsupport from the literature were used to develop the 23 hypotheses shown in Figure 1.Owing to space limitations, the long discussions on the formulation of each of thesehypotheses have been omitted. The one-headed arrows in the model imply ahypothesized direct effect from one factor to another.Model factors IndicatorsLeadership (F1) Top management commitment and leadership (V1),supervisory leadership (V2), public responsibility andcitizenship (V3)Strategic planning (F2) Quality mission, goals and policy (V4), strategy development(V5), strategy deployment (V6)Customer focus (F3) Customer and market knowledge (V7), attention to customersatisfaction (V8), management of customer relationships (V9)Information and analysis (F4) Performance measurement and analysis (V10), informationmanagement (V11), use of information technology (V12),quality tools (V13), benchmarking (V14)Human resource management (F5) Work systems (V15), employee training (V16), employeesatisfaction (V17)Process management (F6) Product and service design (V18), process control (V19),innovation and continuous improvement of processes, productsand services (V20)Supplier management (F7) Supplier quality (V21), supplier involvement (V22), supplierrelationships (V23)Business results (F8) Human resource results (V24): employee turnover rate,employee absenteeism, number of employee suggestionsreceived, employee job performanceCustomer results (V25): customer retention, reliability andtimely delivery of products and services, personalized service,value for the money spentOrganizational effectiveness (V26): cost, quality, productivity,cycle times, number of errors or defects, supplier performanceFinancial and market results (V27): market share, profit, returnon total assets (ROA), overall competitive position, number ofsuccessful new product and service introductionsTable II.TQM factors constitutingthe modelIJOPM25,111128MethodologySurvey instrumentA survey instrument that had a 1-7 Likert scale was designed using an extensiveliterature review. The initial version of the questionnaire was pilot tested byconducting interviews with the general managers of several companies and edited forcomprehensibility and accuracy. The instrument was then reviewed by the ExecutiveFigure 1.The proposed latentvariable modelCritical linkagesamong TQMfactors1129MBA students at a major public university and modified further. Finally, the resultinginstrument was reviewed by quality experts, who were the examiners of a state qualityaward, and revised further to make sure that the measures were valid, reliable, anduser-friendly (Flynn et al., 1990). The total number of items that remained in the finalversion of the questionnaire was 133 (Appendix).SampleThe survey was mailed to 1,500 manufacturing companies operating in the UnitedStates. These companies were randomly selected from the American Society forQuality (ASQ) mailing list using the following Standard Industrial Classification(SIC) codes: 28 (chemicals and allied products), 34 (fabricated metal products), 35(industrial and commercial machinery and computer equipment), 36 (electronic andother electric equipment), 37 (transportation equipment), and 38 (measure, analyzeand construction industries). Of the 1,500 mailed surveys, four were returned asundeliverable. Within one month of mailing, 226 completed surveys were returned.Six of these returned surveys were not usable due to missing data and were,therefore, excluded from the analysis. Thus, the sample for the study consisted of220 manufacturing companies. Table III provides a descriptive summary of therespondents.To test for non-response bias, using the practice of Kannan et al. (1999), the returnedsurveys were divided into two groups: those received early (153 surveys) and thosereceived late (67 surveys). It was assumed that the surveys that were returned laterepresented non-respondents. T-tests were conducted between the two groups on meanresponses to ten questions that were selected randomly. The t-tests showed that therewas no significant difference between the two groups. The two groups were also notsignificantly different in terms of sales, number of employees, and unionization. Thus,these analyses showed that there was no evidence of non-response bias in the data.Industries (SIC codes) Chemicals and allied products (28): 18Fabricated metal products (34): 86Industrial and commercial machinery andcomputer equipment (35): 15Electronic and other electric equipment (36): 75Transportation equipment (37): 12Measure, analyze and construction industries(38): 14Job titles Vice President: 13, General Manager: 3, QualityManager: 114, OtherType of Manager: 6, Engineer: 36, Coordinator:11, Director: 24, Supervisor: 4, Others: 9Site’s sales (in millions of dollars) 0-1: 5, 2-10: 46, 11-20: 32, 21-50: 39, 51-100: 30101-500: 36, 501-1,000: 12, Over 1,000: 12Unspecified: 8Number of employees at the site 0-20: 14, 21-100: 70, 101-500: 89, 501-1,000: 311,001-2,500: 14, 2,501-5,000: 1, Over 5,000: 1Number of hours of continuousimprovement-related training received by anaverage employee0-10: 133, 11-20: 37, 21-30: 13, 31-40: 12, 41-50: 3Over 50: 4, Do not know: 11, Unspecified: 7Over50: 4, Do not know: 11, Unspecified: 7Table III.A profile of therespondentsIJOPM25,111130Analysis and resultsData preparationAs mentioned before, there are a total of 133 items in the questionnaire measuring eightconstructs with a total number of 27 indicators. Each latent construct is measured by atleast three indicators, and each indicator is measured by at least two items. Eachindicator is a parcel, which is simply the average of responses on items correspondingto an indicator. The use of parcels reduced the 133 items to a manageable level. It alsoprovided indicators with higher reliability than that of single items (Rushton et al.,1983).Validity and reliabilityBefore a latent variable model analysis is conducted, the validity and reliability of theconstructs must be assessed. The unidimensionality and reliability of the scales mustalso be established before their convergent and discriminant validity are assessed(Anderson and Gerbing, 1982).UnidimensionalityUnidimensionality measures the extent to which the items in a scale all measure thesame construct (Venkatraman, 1989). Confirmatory factor analysis (CFA) can be usedto assess unidimensionality. A CFA was conducted for each of the eight constructs todetermine whether the 27 indicators measured the construct they were assigned toadequately. Maximum likelihood estimation was employed to estimate the eight CFAmodels. The SEM program EQS for Windows 6.0 was used throughout the study toconduct the analyses.Empirical evidence in CFA (and SEM in general) is generally assessed using criteriasuch as the comparative fit index (CFI), the root-mean square of approximation(RMSEA), the significance of parameter estimates, and the amount of explainedvariance. Table IV summarizes the results of these tests.CFI. This index compares a proposed model with the null model assuming thatthere are no relationships between the measures. CFI values close to 1 are generallyaccepted as being indications of well-fitting models (Raykov and Marcoulides, 2000).A CFI value greater than 0.90 indicates an acceptable fit to the data (Bentler, 1992). TheCFI values for the eight CFAs are displayed in Table IV. An analysis of the tablereveals that all the CFI values are very high ranging from 0.94 to 1, which suggest verygood model fits.RMSEA. The RMSEA is an index used to assess the residuals. It adjusts theparsimony in the model and is relatively insensitive to sample size. According to Huand Bentler (1999), RMSEA must be equal to or less than 0.08 for an adequate model fit.Table IV shows that all the RMSEA values are below 0.08 and indicate adequate modelfits.Parameter estimates. Table IV shows that all the parameter estimates (i.e. factorloadings) are statistically significant and range from 0.52 to 0.92.Amount of explained variance. Squared factor loadings (analogous to R 2) indicatethe percentage of variance in an indicator explained by a factor. As can be seen fromTable IV, all 27 indicators have satisfactory squared factor loadings rangingfrom 0.272 to 0.840. Thus, based on these indices, all of the eight constructs have verygood fits and are all unidimensional.Critical linkagesamong TQMfactors1131Reliability. The degree of consistency of a measure is referred to as its reliability orinternal consistency. The reliability coefficient, Cronbach’s a (Cronbach, 1951), isgenerally used to test the reliability of a scale. a values of 0.70 or greater are deemed tobe indicative of good scale reliability (O’Leary-Kelly and Vokurka, 1998). TheCronbach’s a for the eight TQM factors range from 0.76 to 0.90, suggesting that theyare all reliable (Table IV).Content (internal) validity. Content validity depends on how well the researchercreated measurement items using the relevant literature to cover the content domain ofthe variable that is being measured (Bohrnstedt, 1983). The selection of items in thisFactors andindicators x2 df p-value CFI RMSEAFactorloading * R 2 Cronbach’s aF1 . 4.27 1 0.00077 0.94 0.0740 0.78V1 0.82 0.678V2 0.82 0.671V3 0.58 0.336F2 3.09 1 0.00072 0.97 0.0630 0.90V4 0.90 0.816V5 0.87 0.750V6 0.85 0.718F3 3.05 1 0.05268 0.98 0.068 0.84V7 0.80 0.643V8 0.82 0.674V9 0.77 0.585F4 5.20 5 0.53829 1.00 0.014 0.88V10 0.92 0.840V11 0.82 0.665V12 0.68 0.465V13 0.71 0.507V14 0.78 0.601F5 2.67 1 0.11501 0.99 0.057 0.78V15 0.77 0.596V16 0.81 0.660V17 0.63 0.396F6 1.06 1 0.41652 1.00 0.0180 0.86V18 0.85 0.724V19 0.80 0.645V20 0.81 0.663F7 4.23 1 0.12974 0.98 0.0420 0.76V21 0.59 0.351V22 0.85 0.717V23 0.75 0.566F8 8.38 2 0.01871 0.98 0.0450 0.80V24 0.79 0.630V25 0.75 0.567V26 0.52 0.272V27 0.78 0.615Note: *All factor loadings were significant at p , 0:001Table IV.Summary ofgoodness-of-fit statisticsfor CFAIJOPM25,111132study was based on an extensive review of the literature, giving a strong contentvalidity to the variables being measured.Convergent validity. The Bentler-Bonett Normed Fit Index (NFI) obtained from CFAcan be used to assess convergent validity. This index measures the extent to whichdifferent approaches to measuring a construct produces the same results (Ahire et al.,1996). According to a rule of thumb, NFI values of 0.90 or greater indicate an adequatemodel fit (Bentler, 1995). Table V shows that all the NFI values are greater than 0.90indicating strong convergent validity.Discriminant validity. Discriminant validity measures the degree to which aconstruct and its indicators are different from another construct and its indicators(Bagozzi et al., 1991). Discriminant validity can be assessed by comparing theCronbach’s a of a scale to its correlations with other model variables. There is evidenceof discriminant validity if the a value is sufficiently larger than the average of itscorrelations with these variables (Ghiselli et al., 1981). Table V shows that thedifference between the a value of each scale and the average correlation of each scalewith the other four scales is adequately large, providing evidence for discriminantvalidity.Criterion-related validity. Criterion-related validity is a measure of how the scales ina survey instrument are associated with an independent measure of the relevantcriterion (Nunnally, 1978). Thus, in this case, the seven factors in the model havecriterion-related validity if they are highly and positively correlated with the businessresults factor (criterion). As shown in Table V, the bivariate correlation between eachof the seven factors and the business results factor exceed the acceptable threshold of0.30 and indicate reasonable criterion validity.Following the validity and reliability analyses described above, a latent variablemodel analysis was conducted to examine the hypothesized relationships among theeight factors.Convergentvalidity Discriminant validity Criterion-related validityFactorsBentler-BonettNFIScale Cronbach’sa – average correlationbetween scalesCorrelation betweeneach of the seven factors andbusiness resultsLeadership 0.934 0.281 0.512Strategic planning 0.964 0.292 0.518Customer focus 0.974 0.334 0.485Information andanalysis 0.991 0.292 0.494Human resourcemanagement 0.986 0.330 0.476Process management 0.997 0.310 0.542Suppliermanagement 0.977 0.308 0.496Business results 0.972 0.469 –Table V.Scale validity analysesCritical linkagesamong TQMfactors1133Latent variable model analysisEQS for Windows 6.0 was employed to examine the relationships among the eightfactors. The latent variable model in Figure 1 was tested using data obtained from the220 companies. The goodness-of-fit indices for this model are displayed in Table VI.The CFI value is 0.92 and indicates an adequate model fit. The RMSEA value is0.0560 and also suggests a well-fitting model. All of the 27 indicators load significantlyon their corresponding factors. In addition, 13 of the 23 hypothesized paths aresignificant as shown in Table VII. The standardized coefficients of these paths and theloadings of the indicators on their factors (all significant) are shown in Figure 2.Finally, the R 2 for the dependent factors range from 0.582 to 0.938 (Figure 2)indicating that a large percentage of the variance in the dependent factors is explainedby the independent factors. Although only the significant direct effects are shown inFit index Valuex2 789.24df 311CFI 0.92RMSEA 0.0560Table VI.Summary ofgoodness-of-fit statisticsfor the latent variablemodelPath Path significance *H1. Leadership ! Strategic planning Significant *H2. Leadership ! Information and analysis Significant *H3. Leadership ! Human resource management Significant *H4. Leadership ! Process management Significant * *H5. Leadership ! Supplier management Significant ***H6. Leadership ! Business results Significant * *H7. Strategic planning ! Customer focus Significant *H8. Strategic planning ! Human resource management NonsignificantH9. Strategic planning ! Business results NonsignificantH10. Customer focus ! Business results NonsignificantH11. Information and analysis ! Strategic planning Significant *H12. Information and analysis ! Customer focus Significant *H13. Information and analysis ! Human resource management Significant *H14. Information and analysis ! Process management NonsignificantH15. Information and analysis ! Supplier management Significant *H16. Information and analysis ! Business results NonsignificantH17. Human resource management ! Customer focus NonsignificantH18. Human resource management ! Process management Significant *H19. Human resource management ! Supplier management NonsignificantH20. Human resource management ! Business results NonsignificantH21. Process management ! Business results Significant *H22. Supplier management ! Process management NonsignificantH23. Supplier management ! Business results NonsignificantNotes: *p , 0:001; * *p , 0:05; ***p , 0:01Table VII.Statistical significance ofpath coefficients for thelatent variable modelIJOPM25,111134Figure 2, the decomposition of significant direct, indirect, and total effects among theeight factors is shown in Table VIII.An analysis of Table VIII shows that, as far as the significant direct effects of afactor on other factors are concerned, leadership and information and analysis are thesources of the majority of these effects. Of the 13 significant direct paths, six of thedirect effects originate from leadership and four of them originate from informationand analysis. One of the three remaining direct effects originates from human resourcemanagement, one from strategic planning, and one from process management.Figure 2.The results of the latentvariable model testCritical linkagesamong TQMfactors1135Effect from Effect to Direct effect Indirect effect Total effectLeadership Strategic planning 0.758 * 0.196 * 0.954 *Leadership Customer focus 0.820 * 0.820 *Leadership Information and analysis 0.764 * 0.764 *Leadership Human resource management 0.265 * 0.537 * 0.802 *Leadership Process management 0.203 * * 0.606 * 0.809 *Leadership Supplier management 0.268 *** 0.537 * 0.805 *Leadership Business results 0.288 * * 0.414 * 0.701 *Strategic planning Customer focus 0.331 * 0.331 *Information and analysis Strategic planning 0.257 * 0.257 *Information and analysis Customer focus 0.660 * 0.085 *** 0.745 *Information and analysis Human resource management 0.703 * 0.703 *Information and analysis Process management 0.531 * 0.531 *Information and analysis Supplier management 0.703 * 0.703 *Information and analysis Business results 0.272 * 0.272 *Human resource management Process management 0.756 * 0.756 *Human resource management Business results 0.387 * 0.387 *Process management Business results 0.511 * 0.511 *Notes: *p , 0:001; * *p , 0:05; ***p , 0:01Table VIII.Decomposition of effectsamong factorsIJOPM25,111136As far as the significant indirect effects among factors are concerned, Table VIII showsthat leadership has an indirect effect on factors including strategic planning, humanresource management, process management, supplier management, and businessresults in addition to its direct effects on these factors. Leadership has only an indirecteffect on customer focus through strategic planning. Information and analysis has bothdirect and indirect effects only on customer focus. This factor has only indirect effectson process management and business results. Among the other factors, only humanresource management has a significant indirect effect on another factor. The indirecteffect of this factor on business results is mediated through process management.Discussion of results and conclusionsThe results show that especially leadership and information and analysis play asignificant role in shaping the quality focus of companies. There is also strong supportprovided by other empirical literature (Wilson and Collier, 2000; Pannirselvam andFerguson, 2001) for the importance of these two factors in effectively managing anorganization.The findings of the current study provide important pointers to managers in termsof managing their organizations for superior performance. First, the study establishesthat TQM factors are holistic in that synergies must be created among them to achievefavorable business results. The study identifies leadership and information andanalysis as the two factors that act as the foundations of these synergies. Therefore, asfar as leadership is concerned, companies need to seek such qualities in their topleaders and supervisors that embrace the organization’s focus on quality and assumeresponsibility for quality and change in all aspects of management including humanresource management, customer relationships, and strategic planning. In the area ofinformation and analysis, organizational resources must be allocated to strengthencapabilities in the use of procedures to monitor key indicators of performance, the useof information technology such as the internet to provide high-quality data andinformation to all stakeholders, the use of quality tools, as well as the use of reliableand user friendly hardware systems and software, and benchmarking.Leadership and information and analysis also have strong implications for acompany’s business results. In other words, the effective implementation of practicesrelated to these factors is likely to result in improved performance. Leadership has bothdirect and indirect effects on business results. However, information and analysis onlyhas an indirect effect on business results that is mediated through human resourcemanagement and process management. Thus, other than leadership, processmanagement is the only factor that has a direct effect on business results.The study also underscores the necessity of building organizational competencies inthe area of human resource management, which is measured by such indicators asemployee training and satisfaction and work systems that cover issues such asemployee participation in quality decisions and empowerment, both top-down andbottom-up communication within the company, and the use of cross-functional teams.This factor has a very high direct effect on process management, highlighting thesignificance of the use of effective human resource practices in designing anddeveloping new products and services and managing processes. It also has importantimplications for improvement of business results because of its indirect effect on thisfactor through process management.Critical linkagesamong TQMfactors1137In the academic context, the current study adds to the body of literature on TQMfactors and their effect on performance. Using SEM as a strong methodology to test 23hypotheses, it reveals that only 13 of the 23 proposed hypotheses are significant in theproposed model. Therefore, the hypothesized relationships must be examined furtherin future studies to determine the reasons as to why some of the bivariate relationshipsthat were claimed to be significant in other studies were empirically non-significant inthe current study. For instance, one of the interesting findings is that, contrary to thewidely-held belief, customer focus has no direct or indirect effects on business results.Wright and Snell (2002) argue that simply having a customer focus and acquiringcustomers may not be sufficient for success since customers can easily be lost if theyhave a bad experience with the products and services, or if the new entrants to themarket attract them. Therefore, companies should strive to attain customer loyalty andretention to achieve improved business results (Wright and Snell, 2002). Thus, futurestudies should use customer loyalty and retention as a mediating variable betweencustomer focus and business results in testing such models. The following sectiondiscusses some of the other issues related to TQM-performance relationships, whichpose important questions for future research.Relationship between TQM factors and business resultsA number of previous studies attempted to examine the relationship between variousTQM factors and performance measures to identify those practices that contributed themost to improved performance. However, most of the relationships tested were simplecorrelations and not in an integrated TQM framework such as the one used in thisstudy. In addition, a wider variety of performance measures were used in this study.As mentioned before, only leadership and process management had positive, directeffects on business results in this study. Table IX lists the nature of a number ofrelationships between various TQM factors and performance measures tested by 22other survey studies. Note that only those TQM factors that were similar to the onestested in the current study were displayed in this table.A general analysis of this table reveals that the total number of significantcorrelations between TQM factors and measures (specified as “positive” or “strongpositive” in the table based on the information given in the articles) is much largerthan non-significant or negative correlations. However, it is very difficult topinpoint visible patterns by comparing TQM factor-performance relationshipsacross these 22 studies and the current study. One of the reasons for this is thedifferent survey instruments and performance measures used in each study. Evenwhen a performance measure in two different studies was assigned the same name(e.g. financial results), an analysis of these studies’ survey instruments revealedthat the items measuring the performance measure in the two studies differed.This makes comparison of the effects of TQM factors on performance acrossdifferent studies difficult. However, one could also argue that, in those cases whenthe performance measure has only one item such as customer satisfaction ormarket share, comparisons across studies might be warranted. For instance,leadership was found to have no relationship with customer satisfaction in Wilsonand Collier (2000) while executive commitment had a positive association with thisperformance measure in Parzinger and Nath (2000). One could also argue that suchdifferences in results could be attributed to differences in the industries surveyed,IJOPM25,111138Study TQM factor (s) Performance measure (s)Nature ofcorrelationFlynn et al. (1994) Quality leadership Percent of products shipped without rework NegativeQuality leadership Perception of quality program’s contribution toplant’s distinctive competencePositiveSupplier relationship Percent of products shipped without rework NoneSupplier relationship Perception of quality program’s contribution toplant’s distinctive competenceNoneCustomer interaction Percent of products shipped without rework NoneCustomer interaction Perception of quality program’s contribution toplant’s distinctive competenceNoneFlynn et al. (1995) Process flow management Perceived quality market outcomes (product andservice quality, customer relations, customersatisfaction)NegativeProcess flow management Percent passed final inspection with no rework NegativeAhire et al. (1996) Top management commitment Product quality PositiveSupplier quality management Product quality PositiveCustomer focus Product quality PositiveInternal quality information usage Product quality PositiveLi (1997) Top management leadership Service quality performance (clinical quality,patient satisfaction, responding to patientrequests, responding to patient complaints)NoneWorkforce development Service quality performance (same as above) PositiveInformation analysis Service quality performance (same as above) PositiveAhire and O’Shaughnessy(1998)Customer focus Product quality StrongPositiveSupplier quality management Product quality StrongPositiveInternal quality information usage Product quality NoneAnderson et al. (1998) Information Operational results (same as above) PositiveSupplier management Operational results (same as above) Positive(continued)Table IX.The relationship betweenTQM factors and variousperformance measuresreported by empiricalstudiesCritical linkagesamong TQMfactors1139Study TQM factor (s) Performance measure (s)Nature ofcorrelationGrandzol (1998) Leadership; process management;customer focusFinancial results, operational results, publicresponsibility, customer satisfaction, employeesatisfactionPositiveTerziovski and Dean (1998) Strategic planning Productivity PositiveStrategic planning Competitive advantage PositiveQuazi et al. (1998) Leadership Business outcomes (profitability, revenue,increase in the number of customers)PositiveInformation and analysis Business outcomes (same as above) NoneStrategic planning Business outcomes (same as above) PositiveManagement of process quality Business outcomes (same as above) PositiveQuazi and Padibjo (1998) Management leadership Quality performance PositiveManagement leadership Customer satisfaction NoneSupplier quality management Quality performance PositiveSupplier quality management Customer satisfaction PositiveProcess management Quality performance NoneProcess management Customer satisfaction NoneDow et al. (1999) Customer focus Product quality PositiveSamson and Terziovski (1999) Leadership Organizational performance (customersatisfaction, employee morale, productivity,defects as a percent of production volume,warranty claims cost as a percent of total sales,cost of quality as a percent of total sales, deliveryin full on time to customers)PositivePeople management Organizational performance (same as above) PositiveCustomer focus Organizational performance (same as above) PositiveStrategic planning Organizational performance (same as above) NoneInformation and analysis Organizational performance (same as above) NegativeProcess management Organizational performance (same as above) NoneKannan et al. (1999) Process management Market share NoneProcess management Customer service PositiveProcess management Product quality Positive(continued)Table IX.IJOPM25,111140Study TQM factor (s) Performance measure (s)Nature ofcorrelationProcess management Competitiveness PositiveRavichandran and Rai (2000) Fact-based management Product quality PositiveFact-based management Process efficiency PositiveWilson and Collier (2000) Process management Financial results (Market share, market sharegrowth, ROI, growth in ROI, ROS, growth in ROS)PositiveProcess management Customer satisfaction (Overall customersatisfaction, customer complaints, customerretention rate, incomplete orders, warranty costs,returns, misshipments)PositiveInformation and analysis Financial results (same as above) PositiveInformation and analysis Customer satisfaction (same as above) PositiveLeadership Financial results (same as above) NoneHuman resource management Financial results (same as above) NoneStrategic planning Financial results (same as above) NoneLeadership Customer satisfaction NoneHuman resource management Customer satisfaction NoneStrategic planning Customer satisfaction NoneCurkovic et al. (2000) Committed leadership All firm performance measures (pre-tax ROA,after-tax ROA, ROI, ROI growth, market share,and market share growth)NoneCommitted leadership Product reliability, conformance to specs, designquality, company reputation, product support,responsiveness to customerPositiveCommitted leadership Product durability, pre-sale customer service NoneSupplier development Market share PositiveSupplier development Pre-tax ROA, after-tax ROA, ROI, ROI growth,market share growthNoneSupplier development Product durability, Conformance to specs, designquality, responsiveness to customerPositiveSupplier development Product reliability, company reputation, pre-salecustomer service, product supportNone(continued)Table IX.Critical linkagesamong TQMfactors1141Study TQM factor (s) Performance measure (s)Nature ofcorrelationCloser customer relationships Market share PositiveCloser customer relationships Pre-tax ROA, after-tax ROA, ROI, ROI growth,market share growthNoneCloser customer relationships Conformance to specs, design quality, companyreputation, product support, responsiveness tocustomerPositiveCloser customer relationships Product reliability, product durability, pre-salecustomer serviceNoneSolis et al. (2000)North region of Mexico Top management support Quality performance (Levels of scrap, rework,throughput time, profitability, costs, productivity,warranty costs, and competitiveness)PositiveCentral region of Mexico Top management support Quality performance (same as above) PositiveMidwest USA Top management support Quality performance (same as above) PositiveNorth region of Mexico Strategic quality planning Quality performance (same as above) PositiveCentral region of Mexico Strategic quality planning Quality performance (same as above) PositiveMidwest USA Strategic quality planning Quality performance (same as above) PositiveNorth region of Mexico Quality information availability Quality performance (same as above) NoneCentral region of Mexico Quality information availability Quality performance (same as above) PositiveMidwest USA Quality information availability Quality performance (same as above) PositiveNorth region of Mexico Supplier quality Quality performance (same as above) PositiveCentral region of Mexico Supplier quality Quality performance (same as above) PositiveMidwest USA Supplier quality Quality performance (same as above) PositiveNorth region of Mexico Customer focus Quality performance (same as above) PositiveCentral region of Mexico Customer focus Quality performance (same as above) PositiveMidwest USA Customer focus Quality performance (same as above) PositiveWoon (2000) Leadership and quality culture Quality and operational results (Product andservice quality results, organization operationalresults, supplier quality results)Strong PositiveUse of information and analysis Quality and operational results (same as above) Strong PositiveStrategic planning Quality and operational results (same as above) Strong Positive(continued)Table IX.IJOPM25,111142Study TQM factor (s) Performance measure (s)Nature ofcorrelationHuman resource development and management Quality and operational results (same as above) Strong PositiveManagement of process quality Quality and operational results (same as above) Strong PositiveCustomer focus and satisfaction Quality and operational results (same as above) Strong PositiveParzinger and Nath (2000) Executive commitment; customer needsassessment; process evaluationCustomer satisfaction, capability maturity modelfor software, ISO 9000-3 compliance, overallsuccessPositiveSun (2000a) Quality leadership Performance index (product quality and customersatisfaction, productivity and profitability, marketposition and competitiveness, employeesatisfaction, environment protection)PositiveStrategic planning of quality Performance index (same as above) PositiveHuman resource development Performance index (same as above) PositiveClose co-operation with customers Performance index (same as above) PositiveSun (2000b) Supplier relationship External performances (same as above) PositiveSupplier relationship Internal performances (Cost and profitability,financial and market increase, employeewell-being, satisfaction, development and worksystem performance)PositiveZhang et al. (2000) Leadership; supplier quality management; visionand plan statement; customer focus24Performance of primary products, conformityrates of primary products, reliability of primaryproducts, durability of primary products, defectrates of primary products, internal failure costs asa percent of annual sales, warranty claims costs asa percent of annual salesPositiveTable IX.Critical linkagesamong TQMfactors1143the size and type of companies (manufacturing vs service) surveyed, and so on. Inthis case, the sample in Wilson and Collier (2000) consisted of only companiesfrom the US automotive industry, whereas Parzinger and Nath (2000) surveyedonly software development sites. It would sound too simplistic to suggest that thereason why the impact of leadership on customer satisfaction in the two studies isdifferent is because of the differences in the type of companies surveyed. This isbecause none of these studies controlled for all the other causes that may haveinfluenced these results. However, these differences do suggest that the importanceof TQM factors may be contingent upon such factors as the industry environment,firm size, and country of origin of companies. Therefore, further research is neededto explore the underlying causes that bring about different performance results indifferent environments and whether the TQM factors’ degree of importance differsfrom one environment to another.Although several cross-country studies were conducted, where the similaritiesand the differences in TQM factors and performance measures across countrieswere analyzed, this is still an area of research in operations management thatneeds to be explored in more detail. Several of these cross-country or replicationstudies (Adam et al., 1997; Rungtusanatham et al., 1998; Solis et al., 2000) foundsimilar patterns of TQM factors across the compared countries. However, theyfound different relationships between the factors and performance measures amongthe compared countries or regions. One could argue that the reason why factorsmostly emerged as common across the compared countries was because of theconviction of companies in the investigated regions that all the TQM factors wereuniversal as suggested by the prescriptive quality management literature. Thus,this belief may have led them to adopt similar practices. This may be one of thereasons why different patterns of relationships between TQM factors andperformance measures in the compared countries were obtained. In other words,certain factors may not be related to certain performance measures in a specificcountry or industry or type of firm simply because they are not applicable withinthat context and thus are not significant predictors of performance. Therefore,these issues must be explored in more detail in future studies since it is crucialthat a company’s resources and efforts be allocated to only those practices thatwill yield best performance for the organization, if at all. One possible way to testthese differences could be through the use of multiple group analysis within aSEM framework, where the significance of paths could be tested using data fromcompanies in different industries and countries.Research limitationsThis study also suffered from several limitations common to survey research and tothe use of SEM. For instance, the data were obtained through mail survey and relied onthe perceptions of the respondents. In addition, no causality has been establishedamong the eight factors. One of the basic requirements of establishing causality istemporal ordering (i.e. a cause must be shown to unambiguously precede an effect)(Bullock et al., 1994). Temporal ordering can only be established by conductinglongitudinal studies. However, like most of the studies conducted in this area, thisstudy also used cross-sectional data, which is not sufficient to establish temporalordering.IJOPM25,111144ReferencesAdam, E.E. Jr (1994), “Alternative quality improvement practices and organizationperformance”, Journal of Operations Management, Vol. 12 No. 1, pp. 27-44.Adam, E.E. Jr, Corbett, L.M., Flores, B.E., Harrison, N.J., Lee, T.S., Rho, B-H., Ribera, J., Samson,D. and Westbrook, R. (1997), “An international study of quality improvement approachand firm performance”, International Journal of Operations & Production Management,Vol. 17 No. 9, pp. 842-73.Ahire, S.L. and O’Shaughnessy, K.C. (1998), “The role of top management commitment in qualitymanagement: an empirical analysis of the auto parts industry”, International Journal ofQuality Science, Vol. 3 No. 1, pp. 5-37.Ahire, S.L., Golhar, D.Y. and Waller, M.A. (1996), “Development and validation of TQMimplementation constructs”, Decision Sciences, Vol. 27 No. 1, pp. 23-56.Anderson, J.C. and Gerbing, D.W. (1982), “Some methods for respecifying measurement modelsto obtain unidimensional construct measurement”, Journal of Marketing Research, Vol. 19No. 4, pp. 453-60.Anderson, J.C., Rungtusanatham, M. and Schroeder, R.G. (1994), “A theory of qualitymanagement underlying the Deming management method”, Academy of ManagementReview, Vol. 19 No. 3, pp. 472-509.Anderson, J.C., Rungtusanatham, M., Schroeder, R.G. and Devaraj, S. (1995), “A path analyticmodel of a theory of quality management underlying the Deming management method:preliminary empirical findings”, Decision Sciences, Vol. 26 No. 5, pp. 637-58.Anderson, R.D., Jerman, R.E. and Crum, M.R. (1998), “Quality management influences onlogistics performance”, Logistics and Transportation Review, Vol. 34 No. 2, pp. 137-48.Australian Manufacturing Council (1994), Leading the Way: A Study of Best ManufacturingPractices in Australia and New Zealand, 2nd ed., Australian Manufacturing Council,Melbourne.Bagozzi, R.P., Yi, Y. and Phillips, L.W. (1991), “Assessing construct validity in organizationalresearch”, Administrative Sciences Quarterly, Vol. 36 No. 3, pp. 421-58.Benson, G.P., Saraph, J.V. and Schroeder, R.G. (1991), “The effects of organizational context onquality management: an empirical investigation”, Management Science, Vol. 37,pp. 1107-24.Bentler, P.M. (1992), “On the fit of models to covariances and methodology to the bulletin”,Psychological Bulletin, Vol. 112 No. 3, pp. 400-4.Bentler, P.M. (1995), EQS Structural Equation Program Manual, Multivariate Software Inc.,Encino, CA.Bohrnstedt, G. (1983), “Measurement”, in Rossi, P., Wright, J. and Anderson, A. (Eds),A Handbook of Survey Research, Academy Press, San Diego, CA.Bullock, H.E., Harlow, L.L. and Mulaik, S.A. (1994), “Causation issues in structural equationmodeling research”, Structural Equation Modeling, Vol. 1 No. 3, pp. 253-67.Cronbach, L. (1951), “Coefficient alpha and the internal structure of tests”, Psychometrica, Vol. 16No. 3, pp. 297-334.Curkovic, S., Vickery, S. and Droge, C. (2000), “Quality-related action programs: their impact onquality performance and firm performance”, Decision Sciences, Vol. 31 No. 4, pp. 885-905.Dow, D., Samson, D. and Ford, S. (1999), “Exploding the myth: do all quality managementpractices contribute to superior quality performance”, Production and OperationsManagement, Vol. 8 No. 1, pp. 1-27.Critical linkagesamong TQMfactors1145Flynn, B.B., Sakakibara, S., Schroeder, R.G., Bates, K.A. and Flynn, E.J. (1990), “Empiricalresearch methods in operations management”, Journal of Operations Management, Vol. 9No. 2, pp. 250-84.Flynn, B.B., Schroeder, R.G. and Sakakibara, S. (1994), “A framework for quality managementresearch and an associated measurement instrument”, Journal of Operations Management,Vol. 11 No. 4, pp. 339-66.Flynn, B.B., Schroeder, R.G. and Sakakibara, S. (1995), “The impact of quality managementpractices on performance and competitive advantage”, Decision Sciences, Vol. 26 No. 5,pp. 659-91.Forza, C. and Filippini, R. (1998), “TQM impact on quality conformance and customersatisfaction: a causal model”, International Journal of Production Economics, Vol. 55 No. 1,pp. 1-20.Ghiselli, E.E., Campbell, J.P. and Zedeck, S. (1981), Measurement Theory for the BehavioralSciences, Freeman, San Francisco, CA.Grandzol, J.R. (1998), “A survey instrument for standardizing TQM modeling research”,International Journal of Quality Science, Vol. 3 No. 1, pp. 80-105.Handfield, R., Ghosh, S. and Fawcett, S. (1998), “Quality-driven change and its effects on financialperformance”, Quality Management Journal, Vol. 5 No. 3, pp. 13-30.Hu, L. and Bentler, P.M. (1999), “Cutoff criteria for fit indexes in covariance structure analysis:conventional criteria versus new alternatives”, Structural Equation Modeling, Vol. 6 No. 1,pp. 1-55.Kanji, G.K. and Wallace, W. (2000), “Business excellence through customer satisfaction”, TotalQuality Management, Vol. 11 No. 7, pp. 979-98.Kannan, V.R., Tan, K-C., Handfield, R.B. and Ghosh, S. (1999), “Tools and techniques of qualitymanagement: an empirical investigation of their impact on performance”, QualityManagement Journal, Vol. 6 No. 3, pp. 34-49.Kaynak, H. (2003), “The relationship between total quality management practices and theireffects on firm performance”, Journal of Operations Management, Vol. 21 No. 4, pp. 405-35.Li, L. (1997), “Relationships between determinants of hospital quality management and servicequality performance a path analytic model”, Omega, Vol. 25 No. 5, pp. 535-45.NIST (2002), Malcolm Baldrige National Quality Award Criteria, US Department of Commerce,National Institute of Standards and Technology, Gaithersburg, MD.Nunnally, J.C. (1978), Psychometric Theory, McGraw-Hill, New York, NY.O’Leary-Kelly, S.W. and Vokurka, R.J. (1998), “The empirical assessment of construct validity”,Journal of Operations Management, Vol. 16 No. 4, pp. 387-405.Pannirselvam, G.P. and Ferguson, L.A. (2001), “A study of the relationships between the Baldrigecategories”, International Journal of Quality & Reliability Management, Vol. 18 No. 1,pp. 14-34.Parzinger, M.J. and Nath, R. (2000), “A study of the relationships between total qualitymanagement implementation factors and software quality”, Total Quality Management,Vol. 11 No. 3, pp. 353-71.Quazi, H.A. and Padibjo, S.R. (1998), “A journey toward total quality management through ISO9000 certification – a study on small- and medium-sized enterprises in Singapore”,International Journal of Quality & Reliability Management, Vol. 15 No. 5, pp. 489-508.Quazi, H.A., Jemangin, J., Kit, L.W. and Kian, C.L. (1998), “Critical factors in quality managementand guidelines for self-assessment: the case of Singapore”, Total Quality Management,Vol. 9 No. 1, pp. 35-55.IJOPM25,111146Rao, S.S., Raghunathan, T.S. and Solis, L.E. (1997), “A comparative study of quality practices andresults in India, China, and Mexico”, Journal of Quality Management, Vol. 2 No. 2,pp. 235-50.Ravichandran, T. and Rai, A. (2000), “Quality management in systems development: anorganizational system perspective”, MIS Quarterly, Vol. 24 No. 3, pp. 381-415.Raykov, T. and Marcoulides, G.A. (2000), A First Course in Structural Equation Modeling,Lawrence Erlbaum Associates, Mahwah, NJ.Rungtusanatham, M., Forza, C., Filippini, R. and Anderson, J. (1998), “A replication study of atheory of quality management underlying the Deming management method: insights froman Italian context”, Journal of Operations Management, Vol. 17 No. 1, pp. 77-95.Rushton, J.P., Brainerd, C.J. and Pressley, M. (1983), “Behavioral development and constructvalidity: the principle of aggregation”, Psychological Bulletin, Vol. 94 No. 1, pp. 18-38.Samson, D. and Terziovski, M. (1999), “The relationship between total quality managementpractices and operational performance”, Journal of Operations Management, Vol. 17 No. 4,pp. 393-409.Saraph, G.V.P., Benson, G. and Schroeder, R.G. (1989), “An instrument for measuring the criticalfactors of quality management”, Decision Sciences, Vol. 20 No. 4, pp. 810-29.Solis, L.E., Raghunathan, T.S. and Rao, S.S. (2000), “A regional study of quality managementinfrastructure practices in USA and Mexico”, International Journal of Quality & ReliabilityManagement, Vol. 17 No. 6, pp. 597-614.Sun, H. (2000a), “A comparison of quality management practices in Shanghai and Norwegianmanufacturing companies”, International Journal of Quality & Reliability Management,Vol. 17 No. 6, pp. 636-60.Sun, H. (2000b), “Total quality management, ISO 9000 certification and performanceimprovement”, International Journal of Quality & Reliability Management, Vol. 17 No. 2,pp. 168-79.Terziovski, M. and Dean, A. (1998), “Best predictors of quality performance in Australian serviceorganizations”, Managing Service Quality, Vol. 8 No. 5, pp. 359-66.Venkatraman, N. (1989), “Strategic orientation of business enterprises: the construct,dimensionality and measurement”, Management Science, Vol. 35 No. 8, pp. 942-62.Wilson, D.D. and Collier, D.A. (2000), “An empirical investigation of the Malcolm BaldrigeNational Quality Award causal model”, Decision Sciences, Vol. 31 No. 2, pp. 361-90.Woon, K.C. (2000), “Assessment of TQM implementation: benchmarking Singapore’sproductivity leaders”, Business Process Management Journal, Vol. 6 No. 4, pp. 314-30.Wright, P.M. and Snell, S.A. (2002), “Research update”, HR Human Resource Planning, Vol. 25No. 2, pp. 45-54.Zhang, Z., Waszink, A. and Wijngaard, J. (2000), “An instrument for measuring TQMimplementation for Chinese manufacturing companies”, International Journal of Quality &Reliability Management, Vol. 17 No. 7, pp. 730-55.Appendix. Survey instrumentLeadershipTop management leadership and commitment. Top management:(1) takes responsibility for quality performance (Saraph et al., 1989);(2) views improvements in quality as a way to increase profits (Saraph et al., 1989);(3) places more emphasis on quality than cost (Saraph et al., 1989);Critical linkagesamong TQMfactors1147(4) offers incentives to achieve quality goals (Tabak and Jain, 1999);(5) are held responsible for the promotion of quality (Tabak and Jain, 1999);(6) ensures that each new product and service meets customer expectations (Ritz-CarltonMBNQA Application Summary, 1992); and(7) uses quality performance as an incentive to recruit and retain staff (NIST, 2002).Supervisory leadership. Supervisors:(1) try to obtain the trust of employees (Tamimi and Gershon, 1995);(2) promote customer satisfaction (Stock and Hoyer, 2002); and(3) embrace change as part of our organization’s culture (Harrison, 1995).Public responsibility and citizenship.(1) Our top leaders and employees actively support and strengthen our key communities(NIST, 2002).(2) Our top leaders stress the impacts that our organization has on society (Kuei and Madu,1995).Strategic planningMission and policy.(1) Our mission has a clear focus on quality (Carman, 1993).(2) We take a clear long-term view on how to achieve our goals (Anderson et al., 1995).Strategy development.(1) We set and review our short and long-term goals through a comprehensive planningprocess (Samson and Terziovski, 1999).(2) We allocate sufficient resources for the successful implementation of strategies focusedon quality (Ritz-Carlton MBNQA Application Summary, 1992).(3) We direct resources to the requirements and needs of our. customers;. employees; and. suppliers.(Ritz-Carlton MBNQA Application Summary, 1992).Strategy deployment.(1) At each level of the company, teams are assigned to set objectives and devise actionplans (Ritz-Carlton MBNQA Application Summary, 1992).(2) We have an overall action plan measurement system that covers all key deploymentareas and stakeholders (NIST, 2002).Customer and market focusAttention to customer satisfaction.(1) We link customer satisfaction with internal indicators (Black and Porter, 1996).(2) We determine our customers’ satisfaction relative to customers’ satisfaction withcompetitors (Black and Porter, 1996).IJOPM25,111148(3) Employees assume the major responsibility for ensuring customer satisfaction (Ross andGeorgoff, 1991).(4) Customer complaints are used as input to improve our processes (Samson andTerziovski, 1999).Management of customer relationships.(1) Customer requirements are communicated to employees (Samson and Terziovski, 1999).(2) We use various methods to build relationships with customers and to increase repeatbusiness and positive referrals (NIST, 2002).(3) We follow up with customers on products/services and transactions to receive promptand actionable feedback (NIST, 2002).(4) We reset our standards whenever customer needs and expectations change (Ritz-CarltonMBNQA Application Summary, 1992).Customer and market knowledge.(1) Customer information is gathered in a number of ways including. extensive research done on our industry;. our employees’ observations of customer preferences;. surveying customers who have recently used our products and services (Ritz-CarltonMBNQA Application Summary, 1992); and. existing mechanisms or systems for customers to offer suggestions, compliments,and complaints (NIST, 2002).(2) We ensure that the data and information we provide to our customers on the internet are:. reliable;. accurate;. timely; and. secure (NIST, 2002).Information and analysisPerformance measurement and analysis.(1) We collect and analyze organizational performance and cost data to identify and developimprovements (Black and Porter, 1996).(2) We examine customer-related/market data to develop priorities for improvement (Blackand Porter, 1996).(3) We obtain timely quality data (Saraph et al., 1989).(4) Quality data such as error rates and defect rates are available to:. managers; and. employees (Saraph et al., 1989).(5) We develop procedures to monitor key indicators of. site performance;. competitor performance; and. customer satisfaction (Kannan et al., 1999).Critical linkagesamong TQMfactors1149Benchmarking(1) We formally benchmark the best practices and performances of other industries (Ahireet al., 1996).(2) We formally benchmark direct competitors’:. products/services; and. processes (Adam, 1994).Information management.(1) We have information systems that enable the online access and utilization of customerpreference information (Ritz-Carlton MBNQA Application Summary, 1992).(2) We continuously check our work to ensure that customers receive what they want ontime every time (Ritz-Carlton MBNQA Application Summary, 1992).Use of information technology.(1) Our hardware systems and software are reliable and user friendly (NIST, 2002).(2) We keep our information technology current with changing business needs anddirections (NIST, 2002).(3) We use the internet to provide high-quality data and information to. employees; and. suppliers.. customers (NIST, 2002).Quality tools.(1) The following tools are used in quality improvement. brainstorming;. cause and effect/Fishbone diagrams;. flowchart;. gantt chart;. tree diagram;. check sheet;. control charts;. data points;. histogram;. pareto;. process capability;. scatter diagram;. storyboard case study;. starting teams;. maintaining teams;. ending teams/projects; and. effective meetings (Brassard and Ritter, 1994).IJOPM25,111150Human resource managementWork systems.(1) Hourly/non-supervisory employees participate in quality decisions (Saraph et al., 1989).(2) We constantly ensure that employees are aware of quality issues in our site (Saraph et al.,1989).(3) Employee involvement type programs are implemented in our site (Saraph et al., 1989).(4) We recognize and reward our employees for superior quality performance (Saraph et al.,1989).(5) We use cross-functional teams (Ahire et al., 1996).(6) Barriers between departments are eliminated (Samson and Terziovski, 1999).(7) The communication processes in our site are not only “top-down” but “bottom-up” aswell (Samson and Terziovski, 1999).(8) Human resource management policies are aligned with site quality/performance plans(Black and Porter, 1996).(9) We ensure that the data and information we provide to our employees on the internet are:. reliable;. accurate;. timely; and. secure (NIST, 2002).Employee training(1) We give specific work skills training (e.g. technical or vocational) to hourly employees(Saraph et al., 1989).(2) Quality-related training is given to all employees (Saraph et al., 1989).Employee satisfaction.(1) Employees are surveyed formally and regularly to determine their levels of satisfactionand understanding of our quality standards (Ritz-Carlton MBNQA ApplicationSummary, 1992).(2) Our site safeguards the health, safety, and security of our employees (Ritz-CarltonMBNQA Application Summary, 1992).Process managementProduct/service design process.(1) Our product/service specifications are clear (Saraph et al., 1989).(2) Every attempt has been made to ensure that our process design is fail-safe so that thepossibility of employee errors is reduced (Saraph et al., 1989).(3) We seek employee input before we introduce new products/services or makeproduct/service changes (Flynn et al., 1995).(4) We give clear, standardized work or process instructions to employees (Anderson et al.,1995).(5) We strive to interface all design, marketing, operations, and legal functions throughouteach project (Ritz-Carlton MBNQA Application Summary, 1992).Critical linkagesamong TQMfactors1151Process control.(1) We use statistical techniques to control processes (Saraph et al., 1989).(2) Employees engage in self-inspection (Saraph et al., 1989).(3) We continually use internal or external audits to make sure we deliver quality productsand services (Ritz-Carlton MBNQA Application Summary, 1992).Innovation and continuous improvement of processes.(1) Our organizational culture encourages innovation in all aspects of our processes (NIST,2002).(2) We emphasize the continuous improvement of quality in all work processes (Andersonet al., 1995).Supplier managementSupplier quality.(1) The purchasing department assumes responsibility for the quality of incomingproducts/services (Saraph et al., 1989).(2) Our suppliers have an effective system or programs to ensure quality of their productsand services (Saraph et al., 1989).(3) We usually select our suppliers based on quality rather than price or schedule (Kannanet al., 1999).(4) Our suppliers are certified for quality (Flynn et al., 1995):. by our site; and. by other organizations.Supplier relationships.(1) We prefer long-term relations with a few suppliers (Flynn et al., 1995).(2) We give clear specifications to our suppliers (Saraph et al., 1989).(3) We ensure that the data and information we provide to our suppliers on the internet are:. reliable;. accurate;. timely; and. secure (NIST, 2002).Supplier involvement.(1) We seek the active involvement of suppliers in our. new product development process (Flynn et al., 1995); and. product/service quality planning process (Ahire and Dreyfus, 2000).(2) Our suppliers are expected to offer many extra value-added services (Marchetti, 1999).(3) We cooperate with our suppliers to help improve:. quality (Black and Porter, 1996); and. costs (Larson, 1994).IJOPM25,111152Human resource results(1) Employee turnover rate (GAO, 1991; Adam et al., 1997; Paauwe and Richardson,1997).(2) Employee absenteeism (GAO, 1991; Paauwe and Richardson, 1997; McAdam andBannister, 2001).(3) Number of employee suggestions received (GAO, 1991; NIST, 2002).(4) Employee job performance (NIST, 2002).Customer results(1) Customer retention (GAO, 1991; Hendricks and Singhal, 1997; NIST, 2002).(2) Reliability and timely delivery of products/services (Ferdows and Demeyer, 1990;GAO, 1991).(3) Personalized service (Sharma and Gadenne, 2002).(4) Value for the money spent (Dean and Bowen, 1994; Atkins et al., 2002; NIST, 2002).Organizational effectiveness(1) Cost (Deming, 1986; Hendricks and Singhal, 1997).(2) Product/service quality (Deming, 1986; GAO, 1991; Tan et al., 1999).(3) Productivity (GAO, 1991; Huang and Lin, 2002; NIST, 2002).(4) Cycle times (Anderson et al., 1998; Kim et al., 2002; NIST, 2002).(5) Number of errors or defects (GAO, 1991; Hendricks and Singhal, 1997; Rust et al., 2002).(6) Supplier performance (Deming, 1986; Tan et al., 1999; NIST, 2002).Financial and market results(1) Market share (Shetty, 1987; Juran, 1992; Kannan et al., 1999).(2) Profit (Kuei and Madu, 1995; Hendricks and Singhal, 1997; Das et al., 2000).(3) Return on total assets (GAO, 1991; Omachonu and Ross, 1994; Sankar, 1995).(4) Overall competitive position (Mohrman et al., 1995; Kim et al., 2002; Gunasekaran, 2002).(5) The number of successful new product/service introductions (Lee and Zhou, 2000; NIST,2002).Appendix referencesAhire, S.L. and Dreyfus, P. (2000), “The impact of design management and process managementon quality: an empirical investigation”, Journal of Operations Management, Vol. 18 No. 5,pp. 549-75.Atkins, C.H., Dykes, P., Hagerty, J. and Hoye, J. (2002), “How customer performance partnershipscan sharpen your competitive edge”, The Journal for Quality and Participation, Vol. 25No. 3, pp. 22-5.Black, S.A. and Porter, L.J. (1996), “Identification of the critical factors of TQM”, DecisionSciences, Vol. 27 No. 1, pp. 1-21.Brassard, M. and Ritter, D. (1994), The Memory Jogger II: A Pocket Guide of Tools for ContinuousImprovement and Effective Planning, Growth Opportunity Alliance of Lawerance/QPC,Methuen, MA.Critical linkagesamong TQMfactors1153Carman, J.M. (1993), “Continuous quality improvement as a survival strategy: the SouthernPacific experience”, California Management Review, Vol. 35 No. 3, pp. 118-33.Das, A., Handfield, R., Calantone, R. and Ghosh, S. (2000), “A contingency view of qualitymanagement – the impact of international competition on quality”, Decision Sciences,Vol. 31 No. 3, pp. 649-90.Dean, J.W. Jr and Bowen, D.E. (1994), “Management theory and total quality: improving researchand practice through theory development”, Academy of Management Review, Vol. 19 No. 3,pp. 392-419.Deming, W.E. (1986), Out of the Crisis, MIT Press, Cambridge, MA.Ferdows, K. and Demeyer, A. (1990), “Lasting improvements in manufacturing performance: insearch of a new theory”, Journal of Operations Management, Vol. 9 No. 2, pp. 168-83.GAO (1991), Management Practices: US Companies Improve Performance Through QualityEfforts, US Government Printing Office, Washington, DC, GAO/NSIAD-91-190.Gunasekaran, A. (2002), “Benchmarking in logistics”, Benchmarking, Vol. 9 No. 4, p. 324.Harrison, E.L. (1995), “The case for supervisor involvement”, Human Resource ManagementInternational Digest, Vol. 3 No. 2, pp. 12-15.Hendricks, K.B. and Singhal, V.R. (1997), “Does implementing an effective TQM programactually improve operating performance? Empirical evidence from firms that have wonquality awards”, Management Science, Vol. 43 No. 9, pp. 1258-73.Huang, Y-S. and Lin, B.M.T. (2002), “An empirical investigation of total quality management: aTaiwanese case”, The TQM Magazine, Vol. 14 No. 3, pp. 172-81.Juran, J.M. (1992), Juran on Quality by Design: The New Steps for Planning Quality into Goods andServices, The Free Press, New York, NY.Kim, S., Yea, S-H. and Kim, B. (2002), “Shift scheduling for steppers in the semiconductor waferfabrication process”, IIE Transactions, Vol. 34 No. 2, pp. 167-78.Kuei, C.-H. and Madu, C.N. (1995), “Managers’ perceptions of factors associated with qualitydimensions for the different types of firms”, Quality Management Journal, Vol. 2 No. 3,pp. 67-80.Larson, P.D. (1994), “Buyer-supplier co-operation, product quality and total costs”, InternationalJournal of Physical Distribution & Logistics Management, Vol. 24 No. 6, pp. 4-11.Lee, C.Y. and Zhou, X. (2000), “Quality management and manufacturing strategies in China”,The International Journal of Quality & Reliability Management, Vol. 17 No. 8, pp. 876-99.Marchetti, M. (1999), “Only the strongest will remain”, Sales and Marketing Management,Vol. 151 No. 7, pp. 72-7.McAdam, R. and Bannister, A. (2001), “Business performance measurement and changemanagement within a TQM framework”, International Journal of Operations & ProductionManagement, Vol. 21 Nos 1/2, pp. 88-107.Mohrman, S.A., Tenkasi, R.V., Lawler, E.E. and Ledford, G.E. (1995), “Total qualitymanagement: practice and outcomes in the largest US firms”, Employee Relations,Vol. 17 No. 3, pp. 26-41.Omachonu, V.K. and Ross, J.E. (1994), Principles of Total Quality, St Lucie Press,Delray Beach, FL.Paauwe, J. and Richardson, R. (1997), “Strategic human resource management and performance:an introduction”, The International Journal of Human Resource Management, Vol. 8 No. 3,pp. 257-62.IJOPM25,111154Ross, J. and Georgoff, D. (1991), “A survey of productivity and quality issues in manufacturing:the state of the industry”, Industrial Management, Vol. 33 No. 1, pp. 3-10.Rust, R.T., Moorman, C. and Dickson, P.R. (2002), “Getting return on quality: revenue expansion,cost reduction, or both?”, Journal of Marketing, Vol. 66 No. 4, pp. 7-25.Sankar, M. (1995), Self-Assessment Using the Baldrige Criteria, AQSC Professional and TechnicalDevelopment, Milwaukee, WI.Sharma, B. and Gadenne, D. (2002), “An inter-industry comparison of quality managementpractices and performance”, Managing Service Quality, Vol. 12 No. 6, pp. 394-405.Shetty, Y.K. (1987), “Product quality and competitive strategy”, Business Horizons, Vol. 30 No. 3,pp. 46-53.Stock, R.M. and Hoyer, W.D. (2002), “Leadership style as driver of sales peoples’ customerorientation”, Journal of Market-Focused Management, Vol. 5 No. 4, pp. 355-76.Tabak, F. and Jain, B.A. “Critical TQM factors in emerging economies: an empirical investigationof managerial perceptions using exploratory factor analysis”, Paper presented atFifth International Conference of the Decision Sciences Institute, Athens, Greece,pp. 1783-5.Tamimi, N. and Gershon, M. “A tool for assessing industry TQM practice versus the Demingphilosophy”, Production and Inventory Management Journal, Vol. 36 No. 1, pp. 27-32.Tan, K.-C., Kannan, V.R., Handfield, R.B. and Ghosh, S. (1999), “Supply chain management: anempirical study of its impact on performance”, International Journal of Operations &Production Management, Vol. 19 No. 10, pp. 1034-52.(Ismail Sila is an Associate Professor in the Department of Finance and Management Science inthe College of Commerce at the University of Saskatchewan. He has a PhD degree inManagement Science and Operations Management from the University of Rhode Island. Hisresearch interests are in quality management, e-commerce, and supply chain management. Hisprior research has been published in the International Journal of Production Research theInternational Journal of Quality and Reliability Management, and the International Journal ofHospitality and Tourism Administration.Maling Ebrahimpour has a PhD degree in Management Science and Operations Management.He is the Dean of Gabelli School of Business at the Roger Williams University. Dr Ebrahimpourhas worked in different capacities with various companies. His experiences extend to bothmanufacturing and service organizations. His consulting activities reach three continents of Asia,Europe, and America. Professor Ebrahimpour is the recipient of several awards including theShingo Award for Excellence in Manufacturing Research. He has authored or co-authored over 60articles that have been published in scientific journals and proceedings. Most of his work focuseson various issues of quality in both service and manufacturing companies. Furthermore, he hasserved on the editorial review board of several journals such as Journal of Quality Management,Journal of Operations Management, and the International Journal of Production Research.)Critical linkagesamong TQMfactors1155
Get professional assignment help cheaply
Are you busy and do not have time to handle your assignment? Are you scared that your paper will not make the grade? Do you have responsibilities that may hinder you from turning in your assignment on time? Are you tired and can barely handle your assignment? Are your grades inconsistent?
Whichever your reason may is, it is valid! You can get professional academic help from our service at affordable rates. We have a team of professional academic writers who can handle all your assignments.
Our essay writers are graduates with diplomas, bachelor, masters, Ph.D., and doctorate degrees in various subjects. The minimum requirement to be an essay writer with our essay writing service is to have a college diploma. When assigning your order, we match the paper subject with the area of specialization of the writer.
Why choose our academic writing service?
Plagiarism free papers
Timely delivery
Any deadline
Skilled, Experienced Native English Writers
Subject-relevant academic writer
Adherence to paper instructions
Ability to tackle bulk assignments
Reasonable prices
24/7 Customer Support
Get superb grades consistently
Get Professional Assignment Help Cheaply
Are you busy and do not have time to handle your assignment? Are you scared that your paper will not make the grade? Do you have responsibilities that may hinder you from turning in your assignment on time? Are you tired and can barely handle your assignment? Are your grades inconsistent?
Whichever your reason may is, it is valid! You can get professional academic help from our service at affordable rates. We have a team of professional academic writers who can handle all your assignments.
Our essay writers are graduates with diplomas, bachelor’s, masters, Ph.D., and doctorate degrees in various subjects. The minimum requirement to be an essay writer with our essay writing service is to have a college diploma. When assigning your order, we match the paper subject with the area of specialization of the writer.
Why Choose Our Academic Writing Service?
Plagiarism free papers
Timely delivery
Any deadline
Skilled, Experienced Native English Writers
Subject-relevant academic writer
Adherence to paper instructions
Ability to tackle bulk assignments
Reasonable prices
24/7 Customer Support
Get superb grades consistently
How It Works
1. Place an order
You fill all the paper instructions in the order form. Make sure you include all the helpful materials so that our academic writers can deliver the perfect paper. It will also help to eliminate unnecessary revisions.
2. Pay for the order
Proceed to pay for the paper so that it can be assigned to one of our expert academic writers. The paper subject is matched with the writer’s area of specialization.
3. Track the progress
You communicate with the writer and know about the progress of the paper. The client can ask the writer for drafts of the paper. The client can upload extra material and include additional instructions from the lecturer. Receive a paper.
4. Download the paper
The paper is sent to your email and uploaded to your personal account. You also get a plagiarism report attached to your paper.
PLACE THIS ORDER OR A SIMILAR ORDER WITH Essay fount TODAY AND GET AN AMAZING DISCOUNT
The post Measures of quantitative analysis appeared first on Essay fount.
What Students Are Saying About Us
.......... Customer ID: 12*** | Rating: ⭐⭐⭐⭐⭐"Honestly, I was afraid to send my paper to you, but you proved you are a trustworthy service. My essay was done in less than a day, and I received a brilliant piece. I didn’t even believe it was my essay at first 🙂 Great job, thank you!"
.......... Customer ID: 11***| Rating: ⭐⭐⭐⭐⭐
"This company is the best there is. They saved me so many times, I cannot even keep count. Now I recommend it to all my friends, and none of them have complained about it. The writers here are excellent."
"Order a custom Paper on Similar Assignment at essayfount.com! No Plagiarism! Enjoy 20% Discount!"
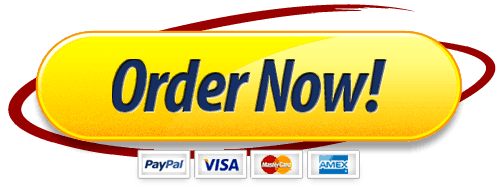