
project about Consider yourself as Global Manager for a Medical Companythe project MUST be supported by evidence and resources
Abstract
Six sigma is a methodology using set of tools and techniques to improve product quality by eliminating or minimizing the causes of defects or errors. Six sigma is implemented in many organization as it is disciplined, data-driven approach and uses methodologies for implementing measurement-based strategy that focuses on process improvement and variation reduction through six sigma projects. All the organization using six sigma projects, uses six sigma levels because it uncovers the layers of process variables in data terms and one should understand and control to eliminate the defects and wasteful costs, whereas in three or four sigma levels, processes deliver too many defects and defects that requires efforts and time leading to poor performance and productivity.
This report is aimed at understanding the significance of six sigma in various industrial settings and presented a case study on various stages of application of six sigma in restaurant industry. Since the performance metrices in service industry is primarily qualitative, it is difficult to measure and eliminate defects compared to manufacturing industries as they are quantitative measurement. This report explains how six sigma projects are used in food industries to improve productivity and how is it is different from manufacturing industry.
Six Sigma in Food Industry
Introduction
In early stages, Total quality management (TQM) was used in business and organizations as a quality improvement program and it is still prevalent in modern industry. Nowadays many companies incorporate six sigma – building on well-proven elements of TQM, as the six-sigma process shows a proven approach for business and industries to improve their overall quality and performances continuously (Seifedine, 2018). The basic difference between TQM and six sigma is the process approach. TQM focus on improving individual business operations whereas six sigma focus on improving overall business operations. Since six sigma is data driven and result oriented, it is applicable to all type of industries.
The Motorola company 1986 was the first to develop and incorporate six sigma to improve their quality by minimizing the defects nearly to zero. Later, six sigma was further introduced to various industrial settings as an initiative to increase the productivity and profitability of the organization (Seifedine, 2018).
Six Sigma – Origin and Evolution
Six sigma was first originated by a Greek philosopher known as Socrates. Socratic method is a learning process to ask series of questions to not only elicit answers but also to encourage thinking (Brue, 2015). Socrates developed this scientific method of identifying causes and solutions to problems using statistical tool and techniques (Brue, 2015). This scientific method with statistical tools is a methodology that describes six sigma.
Six sigma was evolved with the concept of normal curve or normal distribution curve introduced by Carl Friedrich Gauss, an influential mathematician. By repeating a process over again, a set of pattern occurs in the form of bell shape curve as shown in Figure 1. This curve is what known as normal distribution curve used on the basis for analytical and inferential statistics tools to establish the capability of the process (Brue, 2015).
Figure 1: – simple normal distribution curve.
The six-sigma methodology was named based on statistical concept of sigma. The term sigma represents standard deviation which helps to understand how far a process or product can be deviated from a reference of perfection. In other words, it is also known as measure of variation in a process or product. In six sigma, sigma is used to measure the process in terms of number of defects and the number of opportunities for defects. This ratio between defects to opportunities is expressed as Defects per million opportunities (DPMO). The term defects and opportunities for a specific process is defined with the help of DPMO and six sigma (Brue, 2015).
Many organizations use six sigma level instead of three sigma or four sigma because in six sigma, the defects in a process can be identified, measured, and be improved to approach a quality level of zero defects. Whereas in three sigma and four sigma, the process can be achieved with poor quality yielding more defects. The higher the process sigma, lesser the variation in terms of fewer defects. Figure 2 presents the relationship between sigma values and its corresponding process performance and Figure 3 presents a graphical representation of three, four, five and six sigma for a process (Seifedine, 2018).
Figure 2: – Relationship between σ values and its corresponding process performance and capability (Seifedine, 2018).
Figure 3: – Graphical representation of three, four, five, and six sigma in a process (Seifedine, 2018).
Six Sigma -Methodologies
As the goal of six sigma is to produce products with nearly perfectly free from defects, six sigma uses its methodologies known as DMAIC and DMADV to improve the process performance and its productivity. Six sigma DMAIC methodology is a continuous data- driven approach to uncover deviations and to solve problems using the following phases as Define, Measure, Analysis, Improve and Control. The DMAIC methodology is an improvement model and an integral part of six sigma to improve an existing product, process, or service and is a useful framework for six sigma projects. Figure 4 shows DMAIC cycle and how it helps problem- solving more effectively and efficiently.
Figure 4: – DMAIC cycle (Seifedine, 2018).
DMADV is another methodology of six sigma and its phases are Define, Measure, Analysis, Design and Verify. DMADV aims in developing new process or products at six sigma levels whereas DMAIC aims in improving the quality and performance of an existing process or products. The two six sigma methodologies act as tools and techniques to help identify, correct, control the critical to quality (CTQ) elements and minimize or reduce the cost of poor quality (COPQ) (Brue, 2015).
Role of training in Six sigma
Unlike traditional organization, all the employees in six sigma organization need to identify and develop their Skills, Knowledge, and Ability (SKA) to meet the organization requirements and goals. Six sigma uses the concepts of belts borrowed from Martial Arts for training to organize and to designate a level of methodology (Islam, 2006). The belts are in the order of managements hierarchy as Champion belt, Master black belt, Black belt, Green belt, Yellow and white belt. Each belt plays a vital role in the management. In every organizations that incorporate six sigma projects, training, and evaluation of six sigma is very important as it helps in competence building, and factors for employee motivation which in term helps increase in employee’s performance and thus boost employee morale (Pandey, 2007). Figure 5 shows the role of training and its duration for an organization. Among all the belts, black belts are more responsible for executing the six sigma for specific projects. Black belts should be open to change and development in an organization process (Pyzdek & Keller, 2003). They should be proficient in learning to use the advanced and current statistical analysis tool.
Role
Training goal
Duration
Champions Training
Train senior leaders in key concepts of Six Sigma and their role in supporting it in the organization. Training for how to support the green and black belts on their projects and how to pick the projects they work on
Two days
Black Belt
Develop advance skills to conduct development plan for customer satisfaction and productivity improvements
Six months, consisting of four weeks of classroom interspersed with project work (100 percent of person’s time)
Green Belt
Develop skills to drive and plan customer satisfaction and productivity improvements
Ten days to two weeks, over a six-week period, plus project work in between (50 percent of person’s time)
Other team members
Basic training program to link business processes to customer satisfaction leveraging a transaction service business issue to learn tools and techniques.
One-day program
Figure 5: – Role of training in six sigma (Pandey, 2007)
Six sigma – Case studies
As discussed, six sigma can be incorporated in different industrial settings. Since the approach of six sigma is still skeptical and concluded as add-on project management tool, the paper explains how to continue the study on six sigma phenomenon given its acceptance in industries (Desai, 2010). One such industrial setting is service based industries like restaurants, hospitals, finance, education and so on. As six sigma aims in producing products with zero effects, it is difficult to measure the result in term of service industries because the operations are limited by numerous qualitative factors and it requires continuous efforts in achieving those qualities (Brue, 2015).
Six sigma is implemented in service-based industries and the study explores the phenomenon of six sigma implementation, methodologies, principles, and deployment process using various study approach using three different papers and case studies. Its further reviews why empirical study on six sigma is needed and how the research drew conclusion based on characteristics of those case study companies and indicates the success based on the empirical study (Chen & Chen, 2016).
The study by Chen & Chen (2016) discusses the importance of six sigma projects and demonstrate six sigma process and its application. In this work, the theoretical basis of the proposed method and new six sigma DMAIC process were conducted to identify and improve the overall process efficiently and effectively. The case study is based on a campus restaurant in Taiwan to demonstrate the application and methodologies of six sigma. This case study effectively identifies the improvement effectiveness of service speed of the restaurant before and after execution of six sigma project.
As the restaurant systems are important in college campuses, the campus restaurant managers must identify customer needs, reevaluate their market position and improve their product and service quality continuously to satisfy and retain the customers. The manager proposed the idea of incorporating six sigma DMAIC framework and process to improve their quality and productivity effectively and efficiently. Figure 6 shows the improvement framework and process of six sigma DMAIC.
Figure 6: – Improvement framework and process of six sigma DMAIC (Chen & Chen, 2016)
The process is started by gathering the customer complaint data and defining the Critical-to-quality (CTQ) problem statement. The customer complaint data were obtained from complaint forms, phone calls or on location. They used brainstorming and frequency distribution to categorize the complaints from previous months. From the data in figure 7, it shows the top three complaints types are long waiting time (42.50%), food quality defects (19.37%) and missing meal (14.38%). According to 80/20 law, when the most frequent customer complaint is improved, most other service quality problem can be solved. So, six sigma project defined the primary CTQ characteristics as “Long waiting time”.
Figure 7: – Pareto chart of complaint types (Chen & Chen, 2016)
It is measured based on the CTQ problem and questionnaire was designed based on the quality improvement group to investigate and measure the current CTQ performance. The data were collected and customer waiting time was further analyzed by the campus management to reduce the customer complaints. Since, the service speed is crucial CTQ, it requires further analysis to identify the causes for the waiting time by using brainstorming and cause and effect diagram. Figure 8 shows the frequency distribution trend curve before improvement. Figure 9 shows the cause and effect diagram identifying the possible causes for long waiting time.
Figure 8: – Frequency distribution trend curve before improvement (Chen & Chen, 2016)
Figure 9: – Cause-and-effect diagram (Chen & Chen, 2016)
In improve phase, improvement strategies were proposed and displayed using cause and counter measure diagram to improve the core causes as shown in figure 10.
Figure 10: – cause-and-counter measure diagram (Chen & Chen, 2016)
Again, the process was measured using the proposed improvement strategies and ensure the stability of the improved service procedures in control phase. After the proposed improvement strategies, the data were collected and compared before and after long waiting problem. The long waiting time has been reduced from 21.46 minutes (46.50%) to 18.64 minutes (44.62%) respectively. The frequency distribution trend after improvement is shown in figure 11.
Figure 11: – Frequency distribution trend curve after improvement (Chen & Chen, 2016)
From the current study, six sigma DMAIC approach enabled to measure and compare the performances before and after improvement process. Few strategies were proposed during implementation process and could not be implemented because campus restaurant was limited by numerous factors. For example, restaurant could implement real-time application displaying the number of customers in queue in their mobile devices. Evaluate the possibility of installing quick service counter and so on. All these strategies can reduce the waiting time but could not expect to yield an instant result and may require continuous efforts and evaluation. In this case study, six sigma DMAIC provides a feedback loop for improvement which managers should continue to examine the service quality continuously. The current study focused on campus restaurant and the results may not be completely suitable for other types of restaurants. However, it can be used as a reference for similar improvement plans (Chen & Chen, 2016).
One such similar improvement plans is a different case of a campus restaurant in C university in Taiwan. This case study incorporates six sigma using revised Service Quality Performance Matrix (SQPM) approach as a tool in the Define step of six sigma projects (Chen & Chen & Lin, 2012). Using this approach and tool, it helps identifying the Critical-to-quality service dimension and their overall improvement priority to yield a greater service of the restaurant. This paper discusses on using service quality performance matrix to overcome the shortcomings of Performance Evaluation Matrix (PEM) using tools such as standardized indices [0,1], objective Zone and joint confidence intervals of standardized indices. The SQPM is divided into nine quality performance zone and each zone represents different levels of service quality items in a restaurant. For instance, the quality services are represented in a form of matrix and zone represents low satisfaction and importance, Moderate satisfaction and importance and High satisfaction and importance. Figure 12 shows the service quality performance matrix representing different zones and Target zone for measuring customer satisfaction. SQPM approach has been adopted under cost-consideration and to monitor service quality levels.
Figure 12: – Service quality performance matrix (Chen & Chen & Lin, 2012)
According to the case study in campus restaurant in C university in Taiwan, the customers were complaining about the restaurants have increased in frequency which in terms their profit and the service qualities were decreasing. To increase the advance quality and customer satisfactory achievement, revised SQPM approach is used in Define step of six sigma to identify the CTQ problem and proposed improvement strategies and priorities for the restaurant. To find the CTQ problem, a questionnaire was designed to measure the quality performance and overall satisfaction. From the questionnaire, implementation process of revised SQPM was presented as in figure 13. In the measurement phase, the five scales such as food quality, service quality, price and value, atmosphere, and convenience were evaluated by using confirmatory factor analysis tool. Then rating data of the five factors and their quality and satisfaction were collected and calculated. Then from the data, the highest priority for improvement were identified and improved using revised SQPM. The highest priority for improvement from the factors were food quality followed by service quality requiring continuous monitoring for improvement in Define step of six sigma. After the improvement, following MAIC steps should be continued to identify
Figure 13: – Implementation process of revised SQPM (Chen & Chen & Lin, 2012)
the causes of overall poor performance and further take improvement actions. By doing this, the performance-based scale was reduced by 50% and this approach avoided the work of pre-consuming measurement of quality attribute performance. The revised SQPM acts as a primary tool in Define step of DMAIC and provide appropriate service strategies suggestions for overall improvement of the restaurant (Chen & Chen & Lin, 2012).
The above two case studies are the examples of using six sigma projects in food service industries. The third case study discuss the multi-case study approach to compare the similarities and differences of employing six sigma projects in manufacturing and non-manufacturing industries (Nonthaleerak, 2008). The case study was based on nine different companies in Taiwan adopting six sigma process. This approach was selected because of the diversification of business type that enable the research to consider different improvement strategies using six sigma. Then, the data were collected using semi-structured interviews where participants can record their comments freely. With the help of their comments, several protocols were revised and led to the identification of core causes. Then, it is analyzed using data triangulation method by interviewing at least two levels of management and belts professionals in each company. To further analyze the data, the characteristics of the company were studied, and their level of progress and success were assessed. It is considered as a first step in empirical study to understand the issues of comparative practices between the companies. The nine company characteristics are displayed and classified by company size, number of employees and business type in figure 14.
Figure 14: – Company factual data based on company size (Nonthaleerak,2006)
From the figure 14, U.S is the common major shareholder implementing six sigma practitioners. Six sigma is outstanding other quality management by focusing on improving the business performance in terms of increasing the profits. Apart from increasing profits, there are other factors contributing to determine the levels of progress and success using six sigma. After careful analyses, the level of progress and success developed by the companies is indicated in form of matrix as shown in the figure 15.
Figure 15: The matrix of six sigma progress and success in nine companies (Nonthaleerak, 2008)
From the above table, it is clear to determine the implementation aspects of companies leaded to success and aspects been problematic and warrant. From the empirical study, the key findings of the issues were summarized by analyzing the areas of weakness in six sigma implementation, difficulties in implementation process of six sigma and the difference between industry type operations and the issues influencing the success of six sigma. The research further concludes that to enhance and utilize the six sigma, the training materials and weakness in the areas of using DMAIC methodology should be addressed and improved accordingly to the business type.
Conclusion
In summary, based on the case studies, it can be concluded that –
In service industries, the cultivation of an excellent organizational process cannot be achieved within the short period of time and thus it requires continuous monitoring and evaluation.
The application of six sigma in non-manufacturing industrial setting is feasible, however, contexts can also be problematic for many reasons. Lack of data availability is a major concern for the practitioners using six sigma and creates doubts regarding the quality of six sigma incomes.
To overcome those problems, it is always necessary to have in-depth study and training of projects following six sigma methodologies.
Therefore, to conclude, it is always important to improvise the processes by enhancing the project selection criteria, availability of training materials and be particularly aimed in service process improvement irrespective of the industry type.
Reference:
Greg Bure 2015, Six sigma for Managers, McGraw-Hill.
Hsi-Tien Chen and Kuen-Suan Chen 2016, A paired-test method to verify service speed improvement in the Six Sigma approach: a restaurant’s case study.
Kadry, Seifedine 2018, Understanding six sigma concepts, applications and challenges, Nova Science.
K.S Chen, H.T. Chen, and C.L. Lin 2012, Applying a revised SQPM in the Define step of six sigma and a case study.
Islam, K. A. (2006). Developing and Measuring Training the Six Sigma Way: A Business Approach to Training and Development.
Nonthaleerak, Preeprem, Hendry, Linda (2008), Exploring the six-sigma phenomenon using multiple case study evidence.
Pandey, A. (2007). Strategically focused training in Six Sigma way: a case study
PYZDEK, T. (2003). The six sigma handbook. McGraw-Hill.
Get professional assignment help cheaply
Are you busy and do not have time to handle your assignment? Are you scared that your paper will not make the grade? Do you have responsibilities that may hinder you from turning in your assignment on time? Are you tired and can barely handle your assignment? Are your grades inconsistent?
Whichever your reason may is, it is valid! You can get professional academic help from our service at affordable rates. We have a team of professional academic writers who can handle all your assignments.
Our essay writers are graduates with diplomas, bachelor, masters, Ph.D., and doctorate degrees in various subjects. The minimum requirement to be an essay writer with our essay writing service is to have a college diploma. When assigning your order, we match the paper subject with the area of specialization of the writer.
Why choose our academic writing service?
Plagiarism free papers
Timely delivery
Any deadline
Skilled, Experienced Native English Writers
Subject-relevant academic writer
Adherence to paper instructions
Ability to tackle bulk assignments
Reasonable prices
24/7 Customer Support
Get superb grades consistently
Get Professional Assignment Help Cheaply
Are you busy and do not have time to handle your assignment? Are you scared that your paper will not make the grade? Do you have responsibilities that may hinder you from turning in your assignment on time? Are you tired and can barely handle your assignment? Are your grades inconsistent?
Whichever your reason may is, it is valid! You can get professional academic help from our service at affordable rates. We have a team of professional academic writers who can handle all your assignments.
Our essay writers are graduates with diplomas, bachelor’s, masters, Ph.D., and doctorate degrees in various subjects. The minimum requirement to be an essay writer with our essay writing service is to have a college diploma. When assigning your order, we match the paper subject with the area of specialization of the writer.
Why Choose Our Academic Writing Service?
Plagiarism free papers
Timely delivery
Any deadline
Skilled, Experienced Native English Writers
Subject-relevant academic writer
Adherence to paper instructions
Ability to tackle bulk assignments
Reasonable prices
24/7 Customer Support
Get superb grades consistently
How It Works
1. Place an order
You fill all the paper instructions in the order form. Make sure you include all the helpful materials so that our academic writers can deliver the perfect paper. It will also help to eliminate unnecessary revisions.
2. Pay for the order
Proceed to pay for the paper so that it can be assigned to one of our expert academic writers. The paper subject is matched with the writer’s area of specialization.
3. Track the progress
You communicate with the writer and know about the progress of the paper. The client can ask the writer for drafts of the paper. The client can upload extra material and include additional instructions from the lecturer. Receive a paper.
4. Download the paper
The paper is sent to your email and uploaded to your personal account. You also get a plagiarism report attached to your paper.
PLACE THIS ORDER OR A SIMILAR ORDER WITH Essay fount TODAY AND GET AN AMAZING DISCOUNT
The post medical company project appeared first on Essay fount.
What Students Are Saying About Us
.......... Customer ID: 12*** | Rating: ⭐⭐⭐⭐⭐"Honestly, I was afraid to send my paper to you, but you proved you are a trustworthy service. My essay was done in less than a day, and I received a brilliant piece. I didn’t even believe it was my essay at first 🙂 Great job, thank you!"
.......... Customer ID: 11***| Rating: ⭐⭐⭐⭐⭐
"This company is the best there is. They saved me so many times, I cannot even keep count. Now I recommend it to all my friends, and none of them have complained about it. The writers here are excellent."
"Order a custom Paper on Similar Assignment at essayfount.com! No Plagiarism! Enjoy 20% Discount!"
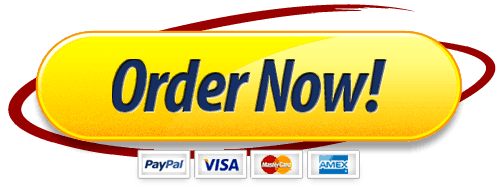